Методы
уменьшения износа деталей
Для
уменьшения износа деталей упрочняют их
поверхность. При ремонте МАХП используют
следующие методы упрочнения:
-
термические;
-
химико-термические;
-
нанесение на поверхность деталей
износостойких материалов (наплавкой,
напылением или гальванизацией);
-
механический наклёп;
-
электроискровое упрочнение.
Методы
упрочнения
Термические
|
Химико-термичес-
кие
|
Нанесение
покрытий
|
Электроискро-вое
упрочнение
|
Пластическое
деформирова-ние
|
-полный
отжиг
-неполный
отжиг
-нормализация
-закалка
(цель - неравн. стр-ра)
-отпуск
(цель - получение более равновесной
структуры)
|
-цемента-
ция
|
-наплавка
-напыление
(10-15мм)
-гуммирование
-гальванизация
(электролитическое наращивание
металла)
а)
хромирование (0.2-0.3мм)
б)
железнение (2-3мм)
в)
никелирование
|
-упрочнение
хромом, графитом
-размерная
обработка (прошивка отверстий)
|
-обкатка
-дробоструйное
упрочнение
|
Термические методы
упрочнения деталей
Термическому
упрочнению подлежат детали,
изготавливаемые из стали, чугуна и
сплавов цветных металлов. Термообработка
осуществляется путём отжига,
нормализации, закалки и отпуска. (Детально
эти виды обработки изучаются в курсе
технологии металлов.)
Из всех методов отжига: полного,
неполного, диффузионного, низкого и
рекристаллизационного в ремонтной
практике применяется в основном: полный
отжиг
(нагрев
до t°
на 30-50°
С выше критической точки по диаграмме
состояний "железо-углерод", выдержка
и последующее медленное охлаждение в
печи, горячем песке или пепле) для
стальных отливок, сварных конструкций,
поковок, штамповок и проката при
повышенных требованиях к механическим
свойствам и микроструктуре металла);
и
неполный отжиг (нагрев стали до t°
на 30-40°C
выше критической, выдержка и медленное
охлаждение) - для сортового проката и
поковок с целью снятия внутренних
напряжений и улучшения обрабатываемости).
Нормализаия,
являющаяся разновидностью полного
отжига, отличается от него выдержкой
детали при нагревании в течении 4-5 часов и
охлаждением на воздухе. Применяется для
деталей из низкоуглеродистой стали с
целью получения мелкозернистой
структуры, улучшения обрабатываемости
резанием и устранения наклёпа после
обработки резанием. Это более быстрая и
дешевая операция в сравнении с отжигом.
Закалка
в ремонтной практике применяется: полная,
неполная, изотермическая, ступенчатая,
прерывистая (для деталей сложной
конфигурации) и поверхностная (электротермическая
и газопламенная). Глубина закаленного
слоя при поверхностной закалке
составляет 1,5-5мм.
Отпуск
– применяют для снятия напряжений,
полученных при закалке. (Нагрев до t<АC1
– до начала образования аустенита,
выдержка, охлаждение с целью превращения
неравновесной структуры в более
равновесную.)
Химико-термическое
упрочнение. Этот метод обработки
поверхности детали изменяет химический
состав металла путём насыщения его
элементами, улучшающими механические
свойства. Такую обработку проводят в
соляных ваннах, в газовых и твердых
средах.
Сущесгвует
несколько методов химико-термического
упрочнения.
Цементация
является процессом насыщения
поверхности детали углеродом для
обеспечения возможности её закалки.
Цементацию осуществляют твердым
карбюризатором (смесь мелких зерен
древесного угля – 85% и одной из
углекислых солей бария, натрия и калия –
15%); жидкостью (в соляных ваннах) или газом
(природным или полученным
путём
разложения бензола, нитробензола или
керосина.)
Ящик
с цементируемыми деталями и
карбюризатором замазывают огнеупорной
замазкой (2 части огнеупорной глины, 1
часть песка, замешанные на воде), помещают
в нагретую печь и выдерживают 8-10 часов
при t°
930-950°С.
В среднем за 1 час поверхность
науглераживается на глубину до 0.15 мм.
Участки, не подлежащие цементации,
защищают меднением или (90% шамотной глины
и 10% асбестового порошка, замешанные на
воде до тестообразной консистенции).
Цементацию
применяют при ремонте зубьев шестерён;
облицовочных пластин прессформ прессов
сухого прессования керамических изделий;
пальцев дезинтеграторов и т.п.
Покрытие
поверхностей трения износостойкими
материалами
К
этому виду обработки относятся: наплавка,
напыление, электроискровое упрочнение и
электролитическое наращивание металла.
Наплавка
является разновидностью сварки и ее
часто применяют при ремонтных работах
для деталей, подверженных образивному
износу. Стойкие к износу наплавки
представляет собой твердые зёрна (карбиды),
вкраплённые в менее твердую, но более
вязкую основу. Наплавку осуществляют
стержневыми, трубчатыми, ячейковыми
электродами, а также порошковыми и
сплошными твердыми сплавами и пастами.
Напылением
могут наноситься покрытия из металла,
пластмасс, резины.
Металлизация
напылением. Достоинства: при этом не
изменяется структура основного
материала, остающегося холодным; толщина
слоя до 10-15 мм, это важно при восстановл.
деталей с большим износом. Недостаток-
малая прочность соединения с пов-тью и
большая трудоемкость.
Напыление
полимерами – эти покрытия имеют высокие
антифрикционные свойства.
Гуммирование
– покрытие деталей резиной. Применяется
для деталей, работающих в образивных или
агрессивных средах (роликов
транспортёров), срок службы которых
вместо 5-6 месяцев возрастает до 5 лет.
Электроискровое
упрочнение. Основан на явлении
электроискрового разряда в цепи
выпрямленного и пульсирующего тока.
Существует
два осн. вида электроискровой обработки:
1.
Электроискровое упрочнение поверхности
детали хромом графитом или разными
сплавами.
2.
Размерная обработка деталей: прошивка
отверстий различной формы в крупных
деталях, крупногабаритных валах (шпоночные
канавки и т.д.) за счёт эрозии (разрушения)
металла электрическим током.
Электролитическое
(гальваническое) наращивание металла.
К
электролитическим методам покрытия
деталей относятся осаждение сплавов,
хромирование, железнение, никелирование,
меднение, цинкование и т.д. Максимальная
толщина покрытия при хромировании 0.2-0.3 мм,
а при железнении 2-3 мм. Объясняется это
тем, что железо осаждается в 10-20 раз
быстрее чем хром.
Упрочнение
деталей поверхностным пластическим
деформированием
Этот
вид упрочнения резко повышает
усталостную прочность деталей и
уничтожает чувствительность
высокопрочных сталей к поверхностным
концентраторам напряжений путём
пластической деформации поверхностных
слоев, что создаёт в них высокие
напряжения сжатия и повышает предел
выносливости поверхностных слоев.
Зона
увеличения твердости проникает на
глубину 0.1-3 мм.
Долговечность
деталей повышается в 1.5–2 раза.
При
ремонтных работах в качестве основных
методов упрочнения деталей
поверхностной пластической деформацией
применяют обкатку и дробеструйное
упрочнение.
Обкатка
осуществляется стальными роликами.
Скорость подачи роликов 0.2-0.8 мм за один
оборот. Кол-во проходов не более 3-4, чтобы
не допустить перенаклёпа.
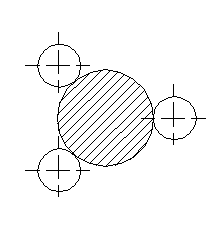
Двумя
Тремя
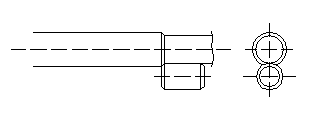
Одним
роликом
Дробеструйное
упрочнение осуществляется путём наклёпа
поверхности готовой детали потоком дроби,
подаваемой специальным дробомётом,
работающим от сжатого воздуха или от
механического привода. Такой обработке
подвергаются закаленные стальные детали,
работающие в условиях знакопеременных
нагрузок (рессоры, пружины, зубчатые
колса). Твердость после обработки
увеличивается на 20-40%, долговечность
возрастает вдвое. Для наклёпа
применяется чугун, реже стальная дробь
диаметра 0.4-2 мм. Скорость полета дроби 50-70
м/с. Длительность обработки от нескольких
секунд до нескольких минут.
Поверхностный
наклёп (обкатка, дробеструйка)
применяется для коленчатых валов,
шестерен, цапф, шатунов и др. деталей из
чугуна, стали и цветных металлов.
Восстановление
деталей.
ВД
применяется при отсутствии зап.частей.
Стоимость ВД обычно составляет 10-25% ст-ти
новой, а для базовых деталей сложной
конфигурации 5-10%.
Выбор
способа восстановленияя опред-ся
величиной и характером износа,
необходимой термообработкой,
конструкционными особенностями,
размерами и характером нагрузок,
действующих на деталь.
Оптимальным
может быть такой способ восстановления
детали, при котором обеспечивается
максимальный срок её службы при
приемлемых затратах. Критерием выбора
оптимального способа восстановления
детали является показатель
эффективности восстановления В:
В
= С / ТП, где
С-
затраты на ремонт
Т-
срок службы после ремонта;
П-
кол-во возможных операций восст-я дет.
Возможны
следующие способы устранения
повреждений деталей:
Сварка
и
|
Для
восстановления и
|
накладки
|
исправления
целостности деталей
|
Наплавка
|
|
Металлизация
|
Для
восстановления
|
Электролитическое
наращивание
|
геометрической
формы
|
Пластическая
деформация (правка, вытяжка, осадка,
раздача, обжатие, накатка)
|
и
размеров деталей
|
Обработка
на ремонтные размеры
|
|
Сварка
Для
ремонтных целей прим-ся разнообразные
способы сварки: дуговая ручная,
электрошлаковая, автоматическая и
полуавтоматическая в углекислом газе и
под флюсом, ацетилено-кислородная и др.
Наиболее распространенная-дуговая
сварка, т.к. позволяет выполнять работы
при любом положении шва. А большой
ассортимент электродов позволяет
подобрать для сварки металл близкий по
механическим свойствам и хим. составу к
основнму металлу.
Сварка
стальных изделий толщиной > 50 мм из
стали, содержащей > 0.23% С осуществляется
с общим местным прогревом до 250-350°
С. При этом используется электроды
диаметром 5,6,8 мм. Сварка осуществляется
от источником постоянного тока при
обратной полярности (деталь соединенная
с положит. полюсом – лучший прогрев). Для
усиления мест сварки ст. деталей могут
использоваться накладки, толщина которых
не должна превышать толщину детали. Перед
сваркой производится разделка кромок до
полного удаления трещин (рубкой,
фрезерованием, проточкой- механические
способы, а также газовой горелкой или
выплавкой электрической дугой).
Трещины
завариваются (после разделки). Если
трещина > 15 мм, устанавливается заплата
, ширина которой должна быть не < 250мм.
Предварительно заплата загибается по
радиусу кривизны корпуса детали (аппарата).
Подготовка
дефекта к сварке
Наплавка
как способ восстановления деталей -
наиболее доступный и распространенный
способ восстановления деталей. Процесс
восстановления детали складывается из
наплавки, отжига и механической
обработки её на номинальный размер.
Наплавка может проводиться на
цилиндрических, плоских и фасонных
поверхностях. Нужная толщина
наплавленного слоя достигается
многослойной наплавкой. Величина слоя -
не ограничена. Износостойкость
наплавленного слоя может быть выше
износостойкости металла детали, если
электроды или присадочные прутки
изготовлены из твердых сплавов.
Недостаток-коробление детали из-за
местного нагрева детали.
Восстановление
деталей методом пластических деформаций
Восстановление
деталей при помощи пластической
деформаций основано на способности
деталей изменять свою геометрическую
форму без разрушения под действием
внешних сил. Используют следующие приёмы
восстановления деталей: правка,
вдавливание, вытяжка, осадка, раздача,
обжатие, накатка и т.д.
Правка
применяется для устранения изгиба,
коробления, скручивание. Этим способом
восстанавливают валы, рычаги, кронштейны,
шатуны. При невозможности правки (стенки
аппарата) устанавливается заплата.
Обжатие
и раздача - (увеличение наружного
диаметра поршневого пальца) для деталей
из пластичных материалов-латуни,
малоуглеродистой стали (при нагреве до
800-900°С)
Для
осуществления пластических деформаций
необходимы специальные приспособления и
штампы. Величина, которую удаётся
компенсировать пластической деформацией
составляет 0.2 мм.
Износостойкость
поверхности детали восстановление
пластической деформации ниже, чем у новой
детали, поэтому этот способ
восстановления используется для
неподвижных соединений, работающих в
лёгких условиях.
Пластическое
деформирование
Правка.
Правку деталей выполняют статическим
нагружением или наклёпом. При правке
статическим нагружением с помощью пресса
к детали прикладывают нагрузку или
крутящий момент, совпадающий по
направлению с направлением требуемой
деформации.
Сущность
правки наклёпом состоит в том, что при
ударах молотком со сферическим бойком по
поверхности детали создаются напряжения
сжатия, которые её выпрямляют. Размер
участков наклёпа и глубину наклёпанного
слоя определяют
При
больших прогибах правку проводят с
предварительным прогревом.
Осадка - для уменьшения
внутреннего и увеличения наружного
диаметра полых и сплошных деталей.
Площадь поперечного сечения детали
увеличивается, а высота (длина)
уменьшается. Осадкой восстанавливают
втулки верхней головки шатунов и
шкворней, вилки карданных валов,
толкатели двигателей.
Вытяжка
и растяжка - для увеличения длины деталей
(тяг, штанг, шатунов, рычагов) за счёт
уменьшения её поперечного сечения. При
вытяжке направление деформирующей силы
P
(рис. б) не совпадает с направлением
деформации, а при растяжке - совпадает.
Раздача
- для увеличения наружных размеров полых
деталей за счёт увеличения их внутренних
размеров. Она характеризуется
совпадением деформирующей силы P
(рис. в) с направлением деформации d.
После этой операции наружный диаметр
детали должен быть равен номинальному
диаметру с учётом припуска на
механическую обработку.
Если
деталь закалена или цементирована, то
перед раздачей её подвергают отжиму или
высокому отпуску.
Обжатие
(рис. г) - для уменьшения внутренних
размеров полых деталей за счёт
уменьшения наружных (обратно раздаче);
-
для восстановления втулок из цветных
металлов и др.
Вдавливание
- объединяет в себе осадку и раздачу, т.к.
деформирующая сила P
направлена под углом к напр-ю деф-ции d.
Длина детали не изменяется.
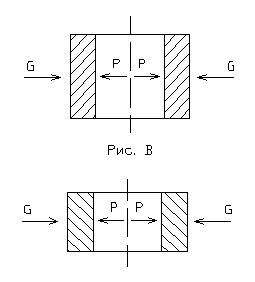
Рис.
г
Накатка
- для увеличения наружного или уменьшения
внутреннего диаметра деталей
вытеснением металла отдельных участков
рабочих поверхностей. Напр-е P
противоположно d
(рис. е).
Обработка
деталей на ремонтные размеры
Обработка
на ремонтные размеры применяются для
сопрягаемых деталей с целью
восстановления посадки в соединении. При
таком виде ремонта одна из сопрягаемых
деталей обрабатывается для устранения
следов износа, (т.е. восстановление только
качество и форма поверхности, а размер
детали изменился). Вторая деталь целиком
изготавливается заново, но уже на новый
размер, обеспечивающий проектную посадку
в соединении.
Например,
для пары вал-втулка. При увел. зазора в
сочлененная шейка вала протягивается для
устранения эллипсности, удаления следов
износа, а отверстие (втулка)
изготовляется заново с меньшим, чем
первоначальное, значение диаметра. Новые
размеры деталей соединения отличаются от
проектных (номинальных) значений и
называется ремонтными. Такой вид ремонта
может применяться несколько раз при
допустимом уменьшении диаметра вала на 10%
от его первоначального размера.
|