Износ
машин и аппаратов и борьба с
ним
При
эксплуатации машин и аппаратов
очень важно дать правильную
оценку износа деталей и
своевременно определить
необходимость ремонта, т.к. при
достижении предельного износа
деталей дальнейшая
эксплуатация машины
становится экономически
нецелесообразным.
Износ
оборудования происходит под
воздействием механических,
тепловых и химических
факторов. Соответственно
различают: механический,
механико-коррозионный и
усталостный износ. Это
неизбежный естественный
процесс. Он проявляется в
пластической деформации
поверхности, изменении свойств
материала в поверхностном слое
детали и т.д. Большое влияние на
такой износ оказывают силы
трения, возникающие при
взаимном перемещении
сопряженных деталей. Вид
износа, обусловленный силами
трения, считается основным (так
называемый механический износ)
Задача
правильной эксплуатации
машины заключается в
обеспечении условий,
уменьшающих скорость износа.
При нарушении нормальных
условий эксплуатации машины
скорость износа возрастает и
наступает аварийный режим.
Помимо механического износа
имеет место старение
материалов, которое
проявляется в
самопроизвольном изменении
строения и свойств материалов
(так называемое естественное
старение). При старении
происходит диффузионное
перемещение атомов в металле
(т.е. изменяется
кристаллическая структура
металла), распад структур,
полученных при термообработке
и превращения,
сопровождающийся изменением
химического состава.
Факторы,
влияющие на износ оборудования
Механические (силы
трения)
|
Тепловые
|
Химические
|
- качество металла
- чистота
обработки
- наличие и
кол-во смазки
|
тепловое
разрушение деталей и их
деформация как следствие
ползучести металла
|
Коррозионный износ
(пластические деформации,
изменение свойств
материала и т.д.)
|
Результат
износа проявляется в изменении
размеров или формы детали,
нарушении ее целостности,
появлении задиров, царапин,
трещин. Косвенными признаками
износа являются снижение
показателей работы машины,
появление вибраций,
заклинивание и т.д.
Механический
износ в основном зависит от
следующих факторов:
1.качества
металла трущихся поверхностей;
2.чистоты
обработки трущихся
поверхностей (определяет
фактическую поверхность
контакта трущихся деталей);
3.наличия
и качества смазки деталей
трущихся пар.
Рассмотрим
эти факторы более подробно.
1)
Для уменьшения износа
применяются специальные
антифрикционные чугуны,
баббиты, бронзы и другие
материалы. Так в центробежных
насосах контактирующие кольца
(вращающееся и неподвижное)
изготавливаются из стали.
Скорость износа пары
сталь-сталь высока. Замена
одного кольца на чугунное
позволяет значительно
повысить долговечность колец.
Так пара чугун-сталь 3х13
работает на истирание в 2-3 раза
дольше, чем пара сталь-сталь.
С
увеличением твердости
материала износ детали
уменьшается. Поэтому при
замене изношенных деталей
особое внимание следует
уделить проверке качества
закалки, цементации и других
методов повышения
поверхностной твёрдости
материала.
Для
описания процесса износа
используют следующие понятия:
Скорость
изнашивания – абсолютный
износ детали во времени,
выраженный в линейных (мкм/ч),
массовых (Г/ч) или объемных
единицах (мм3/ч).
Интенсивность
изнашивания – это отношение
абсолютного износа к пути
скольжения (в мкм/км). В
безразмерной форме (в м/м)
интенсивность изнашивания (J)
имеет малое численное значение
(J=10-12 - 10-8). Например,
для капрона в диапазоне to
90-120oС J= 5?1О-8.
Интенсивность
линейного изнашивания
(безразмерная величина)
Jh
=h/L, где
h - высота изношенного
слоя; L - длина пути трения.
Интенсивность
массового изнашивания
Jm
= M/FL, где
М- масса изношенного
металла; F - номинальная
поверхность площади трения.
Связь
между Jh и Jm:
Jm
= Jh ? r, где r - плотность
металла.
При
to ? твердость металла, и
для описания зависимости
интенсивности изнашивания от to
используется уравнение
J
= А ? ехр(ВТ), где А, В постоянные.
Для
описания зависимости
интенсивности изнашивания от
удельной нагрузки (давления) Р
обычно применяют степенное
уравнение J = cpn, где с,n -
постоянные.
2.
Чистота обработки определяет в
основном износ в период
обкатки (так как в начале
работы деталей
микронеровности, образованные
на поверхности деталей в
результате предшествующей
механической обработки,
разрушаются и возникает новый
микрорельеф поверхности
соответствующий условиям
взаимного перемещения
элементов пары).
На
рис.1 показано изменение
шероховатости поверхности
деталей во времени при
различной начальной чистоте
обработки.
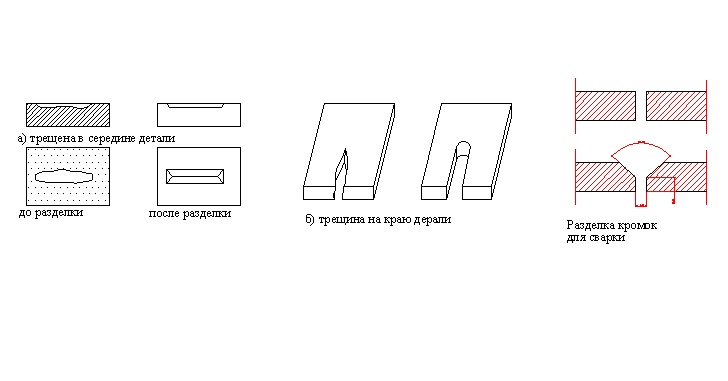
Рис.1
Из
рисунка следует, что
шероховатость поверхности
стремится к установившемуся
значению. Время t1
характеризует период
приработки, т.е. период, когда
наблюдается заметное
изменение шероховатости
поверхности. При t > t1 наблюдается
период установившегося износа.
В этот период коэффициент
трения минимальный и
наблюдается минимальный износ.
Это свидетельствует о том, что
имеется оптимальная
шероховатость. При
изготовлении сменных деталей
необходимо стремиться к
достижению оптимальной
шероховатости, при которой
износ и длительность
приработки деталей будут
минимальными.
Характер
износа деталей во времени
представлен на рис. 2.
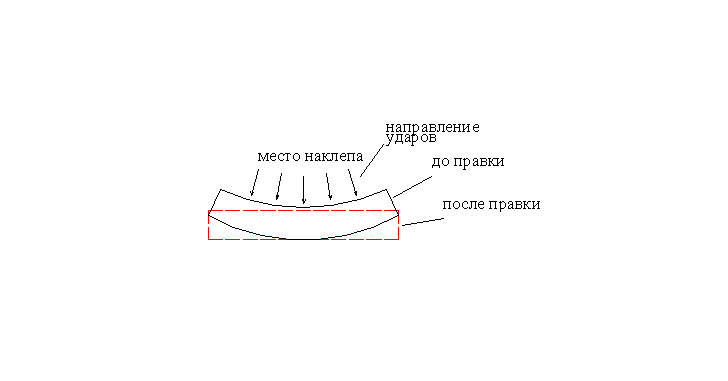
Рис 2.
Где d1 - начальное
значение зазора - зависит от
конструкции соединения.
I
- период приработки (повышенный
износ из-за микронеровностей
от обработки).
II
- период нормального износа
(характеризуется постоянной
скоростью износа). Увеличение
зазора происходит без
заметного снижения
работоспособности.
III
- период аварийного износа,
характеризуется возрастанием
скорости износа.
Зазор
d2 - соответствующий
переходу от II к III является
предельно допустимым. Эти
значения приводятся в
технических условиях на ремонт
машины. В процессе
эксплуатации эти зазоры
периодически контролируются (с
помощью щупа).
(Расчет
деталей на долговечность по
допустимой величине износа
называется расчетом на износ).
Из
кривой износа следует, что
скорость износа в период
приработки уменьшается в
период нормальной
эксплуатации остается
постоянным, в период
аварийного износа
увеличивается.
В
общем виде уравнение износа
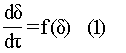
Простейшая
линейная зависимость имеет
вид:
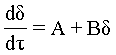
где А и В –
коэффициенты.
Для
I периода В<0. Для II В=О или >1.
Для III В>>1
Процесс
износа является
статистическим, поэтому
уравнение (1) может описывать
кривую износа по средним
значениям зазора или по
максимальным его значениям для
группы одинаковых деталей.
(Распределение зазоров по
размерам подчиняется
нормальному закону).
Для
машины в целом описать ее износ
трудно, поэтому используются
показатели надежности.
3.
Наличие смазки значительно
снижает механический износ,
т.к. при достаточной толщине
смазочного слоя трение деталей
одна о другую заменяется
трением слоев смазки. В
зависимости от толщины и
характера слоя, образуемого
смазкой, возможны следующие
виды трения:
жидкостное
(полное разделение трущихся
поверхностей смазкой);
полужидкое
(смазка покрывает только часть
полной поверхности трущихся
деталей);
полусухое
(большая часть поверхности
деталей не имеет смазки);
сухое
(смазка отсутствует полностью);
граничное
(слой смазки настолько тонок
(менее 0.1 мкм), что его свойства
не подчиняются законам
гидродинамики).
Основные
виды жидких масел,
используемые в качестве
смазок: индустриальные,
автотракторные, авиационные,
трансмиссионные, турбинные,
компрессорные, приборные масла
и масла спец. назначения
(трансформаторные,
гидротормозные и т.д.).
Основными
элементами, для которых
необходима смазка в машинах и
аппаратах, являются подшипники
скольжения зубчатые, цепные,
червячные и винтовые передачи,
сальники, пары трения с
возвратно-поступательным
движением.
Как
конструктивный элемент узла
трения, смазочные масла
выполняют следующие функции:
1.Уменьшают
трение, возникающее между
сопряженными деталями.
2.Снижают
износ и предотвращают задиры
трущихся поверхностей.
3.Отводят
тепло от трущихся
поверхностей.
4.Защищают
трущиеся поверхности от
коррозионного воздействия
внешней среды.
5.Уплотняют
зазоры между сопряженными
деталями.
6.Удаляют
продукты износа и коррозии из
зоны трения.
Коррозионный
износ – процесс разрушения
металлов при химическом или
электрохимическом
взаимодействии их с окружающей
средой. Для аппаратов
химической промышленности
коррозионный износ является
наиболее частой причиной
выхода их из строя. По
характеру разрушений коррозия
может быть сплошной (по всей
поверхности металла) и местной
(в виде отдельных пятен). В
первом случае долговечность
аппарата может быть определена
только с помощью
математической теории
надежности.
В
химической промышленности
отказы аппаратуры
распределяются по видам
коррозии следующим образом:
1)
коррозионное растрескивание –
35%
2)
дырочная коррозия - 20%
3)
общая (равномерная) коррозия -
18%
4)
межкристаллическая коррозия -
16%
5)
другие виды коррозии - 11%
Коррозионное
растрескивание - следствие
двух одновременно действующих
факторов: агрессивности среды
и остаточных напряжений в
металле. Повысить стойкость
аппаратуры из углеродистой
стали к коррозионному
растрескиванию удается
отжигом при 650°C нержавеющих
сталей - отпуском при 650-800°С.
Ремонт
трещин возможен только путем
полного удаления всего
дефектного участка. Попытка
заварить трещину приводит к
раскрытию соседних
микротрещин.
Дырочная
коррозия характеризуется
образованием сквозных
отверстий и наиболее опасна
для аппаратов высокого
давления.
Межкристаллическая
коррозия распространяется по
границам кристаллов или зерен.
Этот вид коррозии опасен тем,
что продукты коррозии остаются
внутри металла, внешний вид
которого не меняется.
В
наибольшей степени коррозии
подвержены:
1)
места с высокой линейной
скоростью среды (например, у
входного или выходного
штуцера);
2)
участки с остаточными
напряжениями (чаще всего-зто
сварные швы);
3)
застойные зоны, где
скапливается жидкость;
4)
зоны нагрева (при повышении
температуры скорость коррозии
резко увеличивается);
5)
узлы трения (механический
износ при воздействии
агрессивной среды усиливается,
изменяются также свойства
смазки).
Расчет
предельного износа
Для
большинства деталей
предельный износ может быть
выражен только допустимым
зазором в сопряжении или
предельно-допустимым
искажением геометрической
формы сопряженных деталей.
Предельный износ в большинстве
случаев определяется
экспериментально. Для
некоторых типовых соединений
машин предельный износ может
быть определен следующим
образом.
Для
пары "вал-подшипник
скольжения" предельный
износ рассчитывается в
зависимости от условий и
режима работы. При жидкостной
смазке, на основании
гидродинамической теории
смазки и накопленного опыта,
наивыгоднейший /оптимальный/
диаметральный зазор.
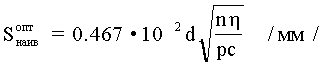
где
d - диаметр шейки вала, /см/
n
- частота вращения вала в 1
минуту;
h
- абсолютная вязкость масла,
Дан с/м2;
пуаз:
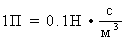
р
- удельное давление на шейку
вала, Дан/м2;
с
- геометрический фактор
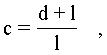
где
l-длина цапфы, /см/
Величина
предельного износа
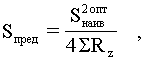
где
SRz - суммарное максимальное
значение высоты неровностей
поверхностей вала и
подшипника, которое зависит от
вида обработки и колеблется в
пределах 0.005-0.01 мм для классов
чистоты Н9-Н10 по стандарту СЭВ
144-75
При
этом предельно допустимый
зазор не должен превышать
величину предельного износа
(ограничение):

Если
подшипник работает в условных
граничного или полусухого
трения, мм:
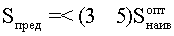
Для
тихоходных валов Sпред =
(0.005 0.002)d /мм/,
а для
быстроходных Sпред = (0.001
0.002)d /мм/.
Допуск
на величину зазора
рекомендуется принимать в
пределах:
Smin
= 0.665 Sоптнаив
Smax
= 1.355 Sоптнаив
|