17. Оборудование для перемещения
продуктов по технологическим схемам.
На предприятиях
химической промышленности технологические трубопроводы являются неотъемлемой
частью технологического оборудования.
Технологические трубопроводы
делятся на внутрицеховые и межцеховые. К. внутрицеховым относятся трубопроводы,
соединяющие отдельные аппараты, установки, машины, расположенные на территории
цеха; к межцеховым - трубопроводы, соединяю-щие оборудование, которое находится
в разных цехах.
В зависимости от расположения
трубопроводы могут быть наземными и подземными. Более распространены наземные
трубопроводы, поскольку легче их технический надзор.
Технологический трубопровод
представляет собой конструкцию, состоящую из ряда элементов: труб,
трубопроводных деталей (фитингов) и арматуры, соединенных разъемными и
неразъемными соединениями. Вследствие большого разнообразия элементов
трубопроводов и значительных объемов их выпуска промышленностью важное значение
имеют вопросы унификации и стандартизации этих элементов. В связи с этим трубы,
трубопроводные детали и трубопроводную арматуру изготовляют, поставляют и
монтируют в соответствии с государственными и отраслевыми
нормативно-техническими документами. Проектирование трубопроводов сводится, в
сущности, к подбору соответствующих трубопроводных элементов по действующим
стандартам и нормалям. При этом важное значение имеют две характеристики
трубопровода - условный проход и условное давление.
Номинальный диаметр отверстия в трубе или арматуре, служащего для
прохода среды, называется условным проходом и обозначается Dу. Если два любых элемента трубопровода имеют одинаковые
значения Dу, то они
имеют одинаковые площади проходного
сечения и одинаковые присоединительные размеры. Ряд условных диаметров
определен ГОСТ 355-67. Для широкого применения в технологических трубопроводах
рекомендуют трубы и арматуру с условными проходами (в мм): 3; 5, 10;, 15; 20;
25; 32; 40; 50; 65; 80; 100; 125; 150; 200; 250; 300; 350; 400; 500; 600; 800;
1000; 1200; 1400; 1600; . 2000; 2400; 3000; 3400; 4000.
Под условным
давлением ру понимают максимальное избыточное давление среды с
температурой 20°С, при котором обеспечивается длительная и безопасная
эксплуатация элементов трубопроводов. При рабочей температуре среды до 200°С
условное давление совпадает с рабочим давлением. При более высокой рабочей
температуре значение условного давления должно быть больше рабочего. ГОСТ
356-68 устанавливает следующий ряд условных давлений (МПа): 0,1; 0,25; 0,4;
0,6; 1; 1,6; 2,5; 4-6,4; 10; 16; 20; 25; 32; 40; 50; 64; 80; 100.
Для объединения
трубопроводов в группы по условиям работы выполнена их классификация с учетом
трех основных параметров: рабочего давления, рабочей температуры, свойств и
параметров перекачиваемой среды.
В
зависимости от свойств транспортируемой среды все техно-логические трубопроводы
делят на пять групп (А, Б, В, Г, Д), а в зависимости от ее параметров (давления
и температуры) - на пять категорий (I, II, III,
IV, V).
Группы А-Д
включают трубопроводы: для токсичных жидких и газообразных продуктов; Б - для
горючих и активных газов, легковоспламеняющихся и горючих жидкостей; В - для
водяного перегретого пара; Г - для водяного насыщенного пара, горячей воды и
парового конденсата; Д - для негорючих газов, жидкостей и паров. В пределах
каждой группы трубопроводы разделены на категории. Так, в группе Б для
перекачивания легковоспламеняющихся жидкостей при температуре 350-700 °С
требуется трубопровод категории I, а при температуре от -150 до +120 °С трубопровод категории
IV. Для трубопроводов
каждой категории установлены определенные нормы проектирования, монтажа,
эксплуатации и ремонта.
В технологических
трубопроводах широко применяют стальные сварные и бесшовные трубы:
горячекатаные, холоднокатаные и холоднотянутые. Сварные трубы можно изготовлять
с продольным или спиральным сварным швом; они менее надежны в. работе, чем
бесшовные. Последние применяют главным образом для транспортирования ядовитых,
взрывоопасных и коррозионно-активных веществ, сварные - во всех остальных
случаях.
Стальные трубы
изготовляют из сталей различных марок, трубы массового назначения - из стали 10
и 20, а трубы специального назначения - из легированных, высоколегированных,
кислотостойких и жаропрочных сталей.
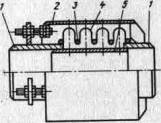
Рис. 17.1 Волнистый
компенсатор
|
Трубы
изготовляют также из чугуна, меди, латуни, свинца, керамики, стекла, фарфора,
пластмассы. В настоящее время трубы из цветных металлов и свинца почти
полностью заменены пластмассами. Из последних наиболее распространены трубы из
винипласта, фаолита, полиэтилена. Эти трубы стойки к агрессивным средам, однако
их можно применять только при невысокой температуре транспортируемой среды.
Так, температурный предел винипластовых труб 40 °С, полипропиленовых труб 100
°С, а труб из фаолита 110°С.
Все более
широко применяют в химической промышленности титановые трубы. Весьма
перспективны стальные трубы с защитным покрытием внутренней поверхности
полиэтиленом, винипластом, эмалью, стеклом и резиной. Наиболее хорошо освоены
отечественной промышленностью трубы, внутренняя поверхность которых покрыта резиной
(гуммированные трубы).
К соединительным деталям
трубопроводов относятся: колена различных конструкций, служащие для изменения
направления трубопроводов; переходы - для изменения площади проходного сечения
трубопровода; тройники, крестовины и развилки для ответвления труб в разные
стороны. Обычно элементы стальных трубопроводов (трубы, колена, переходники)
соединяют сваркой. Если применение сварных соединений в трубопроводах
нецелесообразно, например при необходимости частой разборки соединения, используют
фланцевые соединения с приварными, накидными или резьбовыми фланцами. Наиболее
часто применяют приварные фланцы. Резьбовые фланцы в химической промышленности
устанавливают в основном на трубопроводах высокого давления. Вследствие
разности температур транспортируемых продуктов и окружающей среды трубопроводы
подвержены температурным деформациям. Обычно трубопроводы имеют значительную
длину, поэтому их общая температурная деформация может оказаться достаточно
большой и вызвать разрыв или выпучивание трубопровода. В связи с этим
необходимо обеспечить способность трубопровода компенсировать эти деформации.
Для компенсации
температурных деформаций на технологических трубопроводах применяют П-образные,
линзовые, волнистые и сальниковые компенсаторы.
П-образные
компенсаторы широко применяют для наземных технологических трубопроводов
независимо от их диаметра. Такие компенсаторы обладают большой компенсирующей
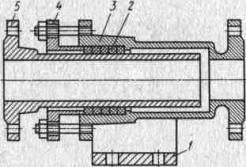
Рис.17.2. Сальниковый компенсатор
|
способностью, их можно применять при
любых давлениях, однако они громоздки и требуют установки специальных опор.
Обычно их располагают горизонтально и снабжают дренажными устройствами.
Линзовые
компенсаторы используют для газопроводов при рабочих давлениях до 1,6 МПа. По
конструкции они аналогичны компенсаторам кожухотрубчатых теплообменников.
Волнистые
компенсаторы (рис. 17.1) используют для трубопроводов с неагрессивными и
среднеагрессивными средами при давлении до 6,4 МПа. Такой компенсатор состоит
из гофрированного гибкого элемента 4, концы
которого приварены к патрубкам 1. Ограничительные кольца 3 предотвращают
выпучивание элемента и ограничивают изгиб его стенки. Снаружи гибкий элемент
защищен кожухом 2, внутри имеет
стакан 5 для уменьшения
гидравлического сопротивления компенсатора.
На трубопроводах
из чугуна и неметаллических материалов устанавливают сальниковые компенсаторы
(рис. 17.2), которые состоят из корпуса 3,
закрепленного на опоре 1, набивки
2 и грундбуксы 4. Компенсация температурных деформаций происходит за счет
взаимного перемещения корпуса 3 и
внутренней трубы 5. Сальниковые компенсаторы, имеют высокую компенсирующую
способность, однако из-за трудности обеспечения герметизации при
транспортировании горючих, токсичных и сжиженных газов их не используют.
Трубопроводы
укладывают на опоры, расстояние между которыми определяется диаметром и
материалом труб. Для стальных труб с диаметром до 250 мм это расстояние
составляет обычно 3-6 м. Для крепления трубопроводов применяют подвески, хомуты
и скобы. Трубопроводы из хрупких материалов (стекла, графитовых композиций и
др.) укладывают в сплошных лотках на сплошных основаниях.
Опоры
могут быть неподвижными и подвижными. Последние обеспечивают компенсацию
температурных деформаций трубопровода. В неподвижных опорах уголки, хомут и башмак жестко связаны между собой, в подвижных опорах вместо нижнего
болта поставлен ролик, который может свободно перемещаться в
отверстиях опорной пластины. Такие опоры необходимо периодически смазывать.