Барабанные
вращающиеся печи для обжига пирита.
Барабан из листовой стали с внутренней
кирпичной футеровкой, марка которого выбирается по предельно допустимой
температуре и кислотности рабочей среды Тепло выделяется за счет происходящей
внутри реакции или с использованием выносной топки.
Во вращающихся барабанных печах обжиг
материала происходит при непосредственном его контакте с газом. Движение
материала противотоком по отношению к газу осуществляется за счет наклона оси
барабана и его вращения. В качестве теплоносителя используется топочный газ,
образующий при горении твердого, жидкого или газообразного топлива.
Используется наружное охлаждение барабана в
зоне реакции.
Это оборудование тяжелое и дорогостоящее.
Основные характеристики: Число оборотов n=0.5¸2 об/мин.; Коэффициент заполнения Кзапол=0.1;
Скорость газа Wгаза<6 м/с (для предотвращения уноса частиц); Диаметр
барабана Dн=1.8¸3.5 м.; Длина до 100 м.; Отношение L/Dн=20¸30.
Таблица 16.1
Основные параметры прямоточных и противоточных
вращающихся печей
Условное обозначение печи
|
Наружный диаметр £>н,
мм
|
Длина L, мм
|
Мощность электродви-гателя N3, кВт
|
Номинальная частота вращения
барабана п,
об/м
|
ПВ 1-8-П; ПВ 1-12-П; ПВ 1-16-П;
|
1000
|
8000 12000 16000
|
3,8 4,8; 0
|
1,62; 2,14; 3,20
|
ПВ 1.2-12П; ПВ 1.2-16П;
|
1200
|
12000 16000
|
|
ПВ 1.6-12П; ПВ 1.6-16П; ПВ 1.6-20П;
|
1600
|
12000 16000 20000
|
0,81; 1,07; 1,62
|
ПВ 2,2- 18П; ПВ 2.2-22П; ПВ 2,2-25
ПВ 2,2-35
|
2200
|
18000 22000 25000
35000
|
7,1; 8,3; 10,5
|
8; 13; 15; 20
|
0,68;
1,01; 1,34; 2,02
|
ПВ 2,5-20 ПВ 2,5-30 ПВ 2,5-40 ПВ
2,5-40-Л
|
2500
|
20000 30000
40000
|
17; 24; 28; 36
|
ПВ 2,8-35 ПВ 2,8-45 ПВ 2,8-55
|
2800
|
35000 45000 55000
|
24; 37,5;
|
ПВ 3-35 ПВ 3-45 ПВ 3-60
|
3000
|
35000 45000 60000
|
55; 75
|
ПВ 3,2-50 ПВ 3,2-60
|
3200
|
50000 60000
|
ПВ 3,5-70
|
3500
|
70000
|
50; 75; 100; 150
|
При производстве цемента встречаются
барабанные печи диаметром до 7 метров и длиной до 230 метров. Толщина
металлической стенки может достигнуть несколько сантиметров.
Недостатки: долго
выводить на режим, относительно малый коэффициент заполнения, дорогостоящий
ремонт.
Вращающиеся
муфельные печи.
Муфельные
печи отличаются от барабанных пламенных печей полным исключением
непосредственного контакта греющих газов с обрабатываемым материалом. Это достигается
специальной футеровкой, выложенной из фасонных силибитных камней (огнеупорный
материал, содержащий до 70% карборунда), образующих один центральный 1 и ряд
периферийных 3 каналов, идущих вдоль всей печи. По центральному перемещается
подлежащий прокаливанию материал, по периферийным каналам - продукты сгорания
топлива, которые отводятся через боковые отверстия 2 в наружной футеровке и
корпусе печи. Разгрузка осуществляется через четыре окна 4.
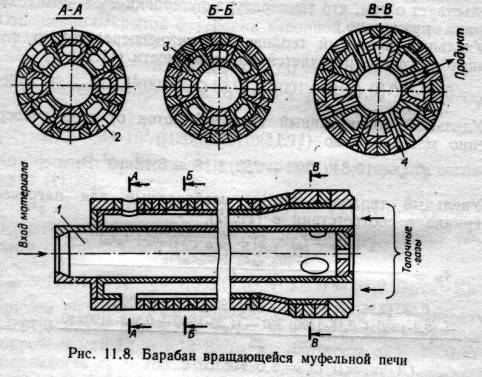
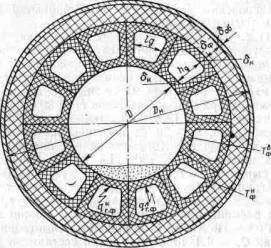
Рис 16.4 Барабан вращающейся муфельной печи
|
Интенсивность
движения материала по печи не должна превышать 7.5¸8.5 см/с, причем число оборотов n принимается в пределах 0.1¸0.4 об/мин и уклон не более 2-4%.
При
определении размеров дымовых каналов предварительно задаются наружным диаметром
печи и принимают толщину стенок фасонных кирпичей, футеровки печи и обечайки.
Скорость движения дымовых газов не должна превышать 10 м/с.
Печи кипящего слоя
(КС).
Интенсивность
обжига серосодержащего сырья определяется, с одной стороны, скоростью реакции
разложения сырья (например, колчедана), скоростью окисления серы и другими
факторами, а с другой стороны, скоростью диффузии кислорода из газового потока
к поверхности сжигаемого сырья, продуктов обжига от поверхности сырья в газовый
поток, а также скоростью отвода тепла от поверхности сырья к газовому потоку,
т.е. процессами массо- и теплопередачи. Поэтому интенсивность обжига сырья в
печах пылевидного обжига выше , чем в полочных печах.
Это объясняется тем, что за счет развитой поверхности
и большой скорости полёта распыляемых частиц сырья увеличивается скорость
процессов тепло- и массоотдачи в печах
пылевидного обжига.
В печах кипящего слоя процессы массо- и теплоотдачи
протекают с ещё большей скоростью, чем в печах пылевидного обжига, так как
частицы сырья интенсивно перемешиваются в турбулентном потоке. Это обусловило в
настоящее время преимущественное распространение печей КС.
Поскольку скорость массо- и теплоотдачи является
важнейшим показателем, определяющим экономику всего технологического процесса,
аппараты с кипящим слоем находят широкое применение в самых разнообразных
отраслях техники.
При движении газа снизу вверх через слой зернистого
твердого материала поведение твердых частиц изменяется с увеличением скорости
газа. Когда скорость газового потока W ниже
критической величины, частицы остаются неподвижными, а высота слоя не
изменяется. С увеличением скорости потока W гидравлическое сопротивление слоя DР возрастает.
Когда W=W'кр, гидравлическое сопротивление слоя становится равным
его силе тяжести (отнесенной к площади сечения решетки), частицы взвешиваются и
приходят в движение. При этом высота слоя увеличивается с Н0 до Н. В
слое наблюдается проскок газовых пузырей, а на его поверхности появляются волны
и всплески. В этом состоянии слой напоминает кипящую жидкость, благодаря чему
он получил название кипящего, взвешенного или псевдоожиженного слоя.
С повышением скорости газа (когда W=W'кр)
высота слоя продолжает увеличиваться, интенсивность движения частиц в слое возрастает
до тех пор, пока скорость газа не достигает второй критической скорости W''кр. Гидравлическое сопротивление слоя при изменении
скорости газа от W'кр до W''кр остается постоянным. Когда W'кр > W''кр, сила
трения газа о частицы превысит силу тяжести слоя и его частицы будут вынесены
из слоя.
Наличие
пика давления Dp в момент перехода слоя к кипящему состоянию вызвано
тем, что для преодоления сил инерции частиц требуются дополнительные усилия.
Гидравлическое сопротивление слоя выражается уравнением:
,
где
DP - гидравлическое сопротивление КС (потеря напора),
кг/м2 (мм вод. ст.)
r - удельный вес огарка, кг/м3
H - высота КС, м
E - порозность слоя (доля объема, приходящаяся на
свободное пространство между частицами)
В
аппаратах постоянного сечения при увеличении W произведение H*(1-E) остается
постоянной, поэтому
, где
H0 -
высота неподвижного слоя, м
E0 -
порозность неподвижного слоя (до его псевдоожижения)
Таким
образом 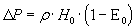
Высокая интенсивность процесса обжига сырья в печи КС объясняется тем, что скорость
процессов массо- и теплоотдачи в кипящем слое значительно выше, чем в
неподвижном слое. Скорость пульсации движущихся частиц в КС обычно составляет
около 10 см/сек, а длина свободного пробега частиц между двумя соударениями
измеряется в мм или в см. При этом движение частиц в вертикальном направлении
происходит более интенсивнее, чем в горизонтальном.
Время пребывания твердых частиц колчедана в кипящем
слое печи может быть охарактеризовано величиной j:
,
где
j - доля колчедана, пребывающего в печи КС в течение
времени больше, чем t.
A - количество колчедана, подаваемого в печь в единицу
времени, кг/ч
b - выход огарка
t - время, ч
O - количество огарка, находящегося в печи, кг
Физико-химический процесс сжигания колчедана в печах
с кипящим слоем.
Печь КС для
обжига колчедана представляет собой вертикальную цилиндрическую футерованную
камеру, в нижнюю часть которой через решетку поступает воздух. Скорость подачи
воздуха регулируют таким образом, чтобы поступающий в печь измельченный
колчедан поддерживался во взвешенном состоянии и не проваливался через решетку.
В печи колчедан очень интенсивно перемешивают с воздухом, что обеспечивает
высокую скорость процесса обжига. Температура во всем объеме кипящего слоя
почти одинакова.
В печах КС можно обжигать не только флотационный, но
и более крупный дробленый колчедан. Если в этом колчедане отсутствует мелочь,
можно увеличить скорость газа и соответственно сжигать большое количество
колчедана на единицу площади решетки. Так, при размере частиц колчедана 6
мм нагрузка печи может достигать 15-20
т сырья на 1 м2 площади решетки в сутки; при сжигании флотационного
колчедана нагрузка уменьшается примерно в два раза.
Количество пыли, уносимой из печей КС, составляет 90% всего огарка. Поэтому вначале запыленный обжиговый
газ проходит через один или два циклона, где отделяется основная масса
наиболее грубой пыли, а затем газ
очищается в электрофильтрах. Благодаря высокой скорости процесса горения и
интенсивному перемешиванию, в кипящем слое находится практически не колчедан, а
огарок. Содержание серы в огарке в различных точках кипящего слоя примерно
одинаково. Высота кипящего слоя определяется высотой, на которой расположено
отверстие для удаления огарка из печи. Продолжительность контакта воздуха с
обжигаемым материалом зависит от высоты кипящего слоя; чем выше кипящий слой,
тем полнее выгорает сера. Для поддерживания большого слоя материала в кипящем
слое следует повысить давление воздуха, подаваемого в печь, приводит к увеличению
расхода электроэнергии.
При обжиге колчедана температура в печах КС, во
избежание слипания частиц сырья не должна превышать 800°C. Потери тепла в окружающуюся среду в этих печах
невелики (1-2% в зависимости от производительности печи), поэтому для поддержания
в них требуемой температуры необходимо отводить из печей большое количество
тепла. Для этого в зоне кипящего слоя располагают охлаждающие элементы -
змеевики для подогрева воды или секции труб парового котла, что позволяет
совместить в одном аппарате процессы сжигания колчедана и получение пара.
Коэффициент теплопередачи в КС составляет около 1000 кДж/(м2×ч×град).
Производительность печи КС - от 14 до 500 т/сутки
сжигаемого сырья при интенсивности до 20 т/сутки на 1 м2 решетки.
Давление пара, получаемого в таких печах, от 24.5 до 123 бар (25-125 ат.),
температура пара до 500°C.
Для обжига цинковых и медных руд и концентратов применяют печи КС, отличающиеся
от описанных выше печей такого типа некоторыми деталями. Это отличие обусловлено
составом обжигаемого сырья, и тем, что главной целью обжига сырья в печах цветной металлургии является
получение качественного огарка, из которого в дальнейшем стремятся получить
возможно полнее цветные металлы. Режим обжига в печах КС цветной металлургии
также отличается от режима обжига сырья в производстве серной кислоты.
Интенсивность печи, отнесенная к единице площади
решетки (кг/(м2×сутки)), у печей КС разной конструкции колеблется в широких пределах, а
интенсивность, отнесенная к общему объему печи (кг/(м3×сутки)), колеблется значительно меньше. Чем выше интенсивность,
отнесенная к единице площади решетки, тем больше свободный объем над кипящим
слоем; при этом условии обеспечивается достаточно полное сжигание серы.
Существенным достоинством метода сжигания колчедана в
кипящем слое является получение также получение концентрированного сернистого
газа (12-15% SO2) с низким содержанием SO3 и при остатке
серы в огарке около 1%.
Благодаря большим достоинствам печей КС, они находят
все более широкое применение в производстве серной кислоты. Новые
сернокислотные системы оборудуются преимущественно печам КС производительностью
200 400 т/сутки колчедана,
механические печи на действующих заводах постепенно заменяют печами КС.
Большой практический интерес представляет печь КС двумя
кипящими слоями, получившая название
ДКСМ. Во втором слое печи ДКСМ происходит окисление остатков серы, содержащейся
в огарке, который выносится газовым потоком из первого (нижнего слоя);
понижение температуры газа, а также сульфатизация огарка, в результате чего
содержащиеся в огарке медь, цинк и некоторые другие цветные металлы переходят в
соли, растворимые в разбавленных растворах серной кислоты.
Ведутся опыты по обжигу колчедана в циклонных печах,
представляющих собой вертикальный футерованный цилиндр, в который по
касательной подается с большой скоростью нагретый воздух со взвешенным в нем
тонко измельченным колчеданом. За счет выделения тепла реакции температура в
печи повышается до 1000-1200°C.
В этих условиях увеличивается скорость выгорания серы, а огарок плавится ,
отбрасывается центробежной силой к стенке печи и , увлекаемый потоком, вытекает
из печи.
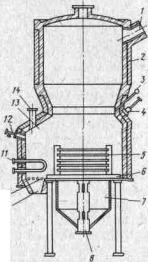
Рис. 16.5.
Печь
кипящего слоя
|
слой обладает текучестью, 'Хорошо
перемешивается и по виду напоминает кипящую жидкость; поэтому он назван
псевдоожиженным или кипящим.
Псевдоожиженный
слой позволяет проводить реакции между газами и твердыми веществами в
интенсивном режиме с хорошим выходом целевого продукта. Мелкозернистость слоя
обеспечивает развитую поверхность контакта между газом и твердым веществом, что
весьма существенно, так как реакция протекает в основном на поверхности твердых
частиц. Интенсивное перемешивание слоя обеспечивает постоянство концентраций и
температуры по объему и позволяет проводить реакцию при оптимальных условиях.
Реакторы
с псевдоожиженным слоем по своим характеристикам близки к аппаратам идеального
смешения и обладают их недостатками. Основной из них - снижение скорости
реакции вследствие f разбавления
реагирующих веществ продуктами реакции - устраняют секционированием аппарата
перегородками с использованием противотока между секциями. Концентрация
твердого реагента в кипящем слое меньше, чем в неподвижном (плотном). При проек-тировании
и эксплуатации приходится учитывать истирание сте-нок аппарата твердыми
частицами, измельчение их при трении одна о другую и унос твердых частиц в виде
пыли с отходящим газом, что требует установки пылеочистного оборудования. По
устройству такие реакторы очень близки к сушилкам с кипящим слоем.
Первая
крупная промышленная установка с использованием псевдоожиженного слоя создана
Ф. Винклером для газификации измельченного угля.
Первый
газогенератор высотой 13 м, площадью поперечного сечения 12 м2
создан в 1926 г. Газогенератор имеет значительный объем, необходимый для подачи
вторичного кислорода в область над слоем. В результате повышается температура и
разлагается выделившийся метан. Аппарат работает при давлении, близком к
атмосферному; несмотря на это по производительности [1,7 т/(кв.м*ч)] он почти
вдвое превосходит газогенератор Лурги. Недостатки газогенератора Винклера -
потребление большого количества кислорода и значительные (более 20 %) потери
углерода вследствие уноса. В связи с переходом промышленности на углеводородное
сырье необходимость в газогенераторах отпала. В будущем, возможно, их вновь
будут использовать. По современным данным, газогенераторы Винклера и Лурги
имеют близкие технико-экономические показатели.