16. Печи в химической промышленности.
Печами называются химические реакторы, работающие при
высоких температурах. Процессы, протекающие в таких реакторах, требуют подвода
и отвода больших количеств тепла и часто осуществляются при высоких давлениях.
Крекинг - наиболее распространенный процесс,
осуществляемый в печах. Это высокотемпературное разложение углеводородного
сырья с получением продуктов меньшей молекулярной массы (например, мазут R бензин). Условия проведения процесса: температура от
4000 до 5000С, давление 60 атм. Это термический крекинг.
Каталитический крекинг осуществляется в аппаратах с
движущимся слоем гранулированного катализатора и используется для получения
высокооктанового бензина.
Пиролиз аналогичен термическому крекингу, но
проводится при более высоких температурах. Повышение температуры позволяет
вести процессы при более низком давлении: температура от 6500 до
12000С и давлении от 2 до 5 атм. Таким способом из углеводородных
газов (пропан - бутан) или бензиновых фракций получают этилен, пропилен,
бутадиен, ацетилен и этилен. Последний используется для производства этилового
спирта, стирола, полиэтилена. Пиролиз осуществляется в змеевиках трубчатых
печей в режиме идеального вытеснения. Трубы обогреваются пламенем горелок (при
использовании газообразного топлива) или форсунок (при использовании жидкого
топлива).
Например, обработка пропано-бутановой смеси
осуществляется в следующих условиях:
конечная температура 10000 - 11000C, давление 1
- 2атм, время реакции 0,7 - 1,5 с, начальная скорость газа 10 - 15м/с, конечная
скорость газа 150 - 200м/с.
В печах так же осуществляются: отжиг клинкера
(производство цемента), известняка, гипса, соды, пирита (производство серной
кислоты).
Сложность процессов, протекающих в печах, можно
проиллюстрировать на примере обжига колчедана.
При обжиге колчедана протекает несколько реакций.
Вначале проходит реакция термического разложения дисульфида железа FeS2 с
образованием сульфида железа FeS и
выделением парообразной серы:
2FeS2 =
2FeS + S2 - 103.9 кДж (24.8 ккал)
Выделение серы начинается при температуре около 500°C и сильно
ускоряется с дальнейшим ее увеличением. Далее пары серы сгорают с образованием
двуокиси серы:
S (газ) + O2 (газ)
= SO2 (газ)
+362.4 кДж (86.5 ккал)
Такая реакция протекает и при сжигании элементарной
серы. Сульфид железа FeS также
сгорает, однако точный механизм этого производства не установлен; предложено
лишь несколько примерных схем реакций.
По одной из них первой стадией окисления FeS является образование сульфатов железа, далее разлагающихся
до окислов железа.
Суммарный процесс горения колчедана протекает с
образованием либо окиси железа: 4FeS2 + 11O2 = 2Fe2O3 + 8 SO2 + 3415.7 кДж (815.2 ккал)
либо закиси-окиси железа
3FeS2+
8O2 = Fe3O4 + 6SO2 + 2438.2 кДж (581.9 ккал)
Благоприятными условиями для образования Fe3O4 являются высокая температура, повышенное содержание
сернистого ангидрида в газе и относительно большое количество несгоревшего колчедана.
Присутствующие в колчедане сульфиды цветных металлов образуют окислы или
сульфаты в зависимости от условий обжига (температуры, содержания в газе O2 и
др.). При наличии карбонатов металлов выделяется двуокись углерода и образуются
окислы соответствующих металлов, которые затем превращаются в сульфаты.
При обжиге углистого колчедана одновременно с серой
сгорает содержащийся в ней углерод: C + O2 = CO2 +409.8
кДж (97.8 ккал)
В этом случае уменьшается содержание O2 в
обжиговом газе, что снижает скорость дальнейшего процесса окисления сернистого
ангидрида на катализаторе.
При окислении колчедана огарком (при температуре
около 800°C) получают
высококонцентрированный сернистый газ:
FeS2
+16Fe2O3 +11Fe3O4 + 2SO2
- 450.8 кДж (107.6 ккал)
Образовавшаяся закись-окись железа окисляется
кислородом воздуха при температуре около 900°C и снова возвращается в процесс:
11Fe3O4 + 2.75O2 = 16.5Fe2O3 + 1279.2 кДж (305.3 ккал)
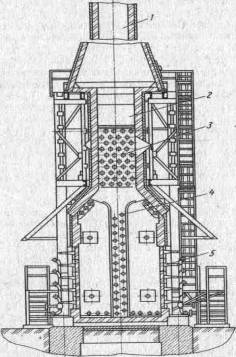
Рис. 16.1. Трубчатая печь с горизонтальными трубами и излучающими
стенками.
|
Классификация печей
1.
Шахтные печи и
газогенераторы (вертикально-цилиндрические реакторы).
2.
Полочные обжиговые
печи.
3.
Барабанные вращающиеся
печи (вращающиеся муфельные печи).
4.
Печи с псевдоожиженным
слоем.
5.
Роторные печи
(периодические с наружным обогревом)
Трубчатые печи.
Трубчатые печи отличаются разнообразием конструкций,
зависящих от вида используемого топлива. Основные элементы печи - стальной
сварной каркас, кирпичная кладка, образующая стены под и свод печи, змеевик,
расположенный внутри, горелки или форсунки для сжигания топлива, дымоход и
дымовая труба. Внутреннее пространство печи разделено обыч-но на две камеры -
радиантную (топочную) и конвекционную, - в
каждой из которых размещены секции змеевика. Ряд труб змеевика,
размещенных в топочной камере и воспринимающих лучистую теплоту горелок,
называют экраном. В радиантной камере сырью
передается основная доля теплоты (около 70 %). К трубам конвекционной секции змеевика теплота подводится от
дымовых газов в основном конвекцией (70 %) и частично лучеиспусканием от
дымовых газов (20 %) и нагретых .стенок камеры (10 %). Дымовые газы движутся
через трубчатую печь обычно под действием естественной тяги, регулируемой
шибером в дымоходе.
В установках
пиролиза используют в основном печи коробчатой формы с горизонтальным
расположением труб змеевика и беспламенными (точнее короткопламенными) газовыми
горелками панельного типа. Нижняя часть боковых стен печи выполнена из
беспламенных панельных газовых горелок, расположенных пятью горизонтальными
рядами в каждой стене и образующих два излучающих блока. В середине топочной
камеры установлен трубный экран двустороннего облучения, делящий камеру на две
половины. В связи с этим печь считают двухкамерной (две камеры радиации). Экран
может быть одно- или двухрядным. Имеются также подовый и потолочный экраны. В
расположенном над топочной камерой дымоходе 2
размещены трубы конвекционной части змеевика 3. Пройдя конвекционную камеру, газы поступают в дымовую трубу.
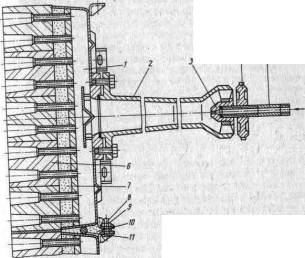
Рис. 16.2. Беспламенная панельная горелка.
|
В
установках пиролиза сырье (пропан-бутановая фракция) после испарения и
предварительного нагревания в теплообмен-нике поступает двумя потоками сначала
в конвекционную часть змеевика печи, а затем в радиантную (т. е. в трубы
экранов). Выходящий из печи пирогаз поступает в закалочный аппарат, где быстрым
охлаждением (впрыскиванием воды) прекращают реак-цию. В печи можно регулировать
теплоотдачу к различным участкам радиантного змеевика подачей топливного газа к
горелкам. Для этого каждый ряд горелок питается независимо от обособленного
коллектора.
Удобные
и высокоэффективные нагреватели для печей - беспламенные панельные горелки
(рис. 16.2), обеспечивающие полное сгорание газа при малом коэффициенте избытка
воздуха благодаря высокой температуре в зоне горения. Горелка имеет
распределительную камеру (короб) 1, в переднюю часть которой вварены трубки для
выхода газовоздушной смеси. На свободные концы трубок надеты керамические
призмы 6, каждая с четырьмя
цилиндро-коническими отверстиями (туннелями). Призмы образуют керамическую
панель размерами 500x500 или 605x605 мм, служащую при горении газа
аккумулятором и излучателем теплоты. Между призмами и стенкой короба расположен
слой теплоизоляции 7 из диатомовой крошки. К задней стенке короба 1 прикреплен
инжекторный смеситель 2 газа (метано-водородной фракции) с воздухом, снабженный
соплом 3 и заслонкой 4. Газ поступает в сопло 3 из патрубка 5. Выходя из сопла с
высокой скоростью, газ инжекти-рует из атмосферы необходимое количество
воздуха. Газовоздушная смесь смесь, образующаяся в смесителе 2, обтекая
отбойник, поступает в короб, откуда распределяется по трубкам (ниппелям)
горелки. Сгорание смеси происходит и в основном завершается в туннелях
керамических элементов, куда смесь поступает из трубок. Для того, чтобы пламя
из туннелей не проскакивало внутрь короба, скорость газовоздушной смеси в
распределительных трубках не должна быть меньше скорости распространения
пламени. В туннелях, благодаря их конической форме, обеспечивается равенство
этих скоростей, что является необходимым условием нормальной работы горелок.
Горелки
соединены между собой болтами 8 с
гайками 9, образуя излучающие стены печей. Зазоры между горелками заполняются
диатомовой крошкой 10 и уплотняются
асбестовым шнуром 11.
Теплопроизводительность
горелок регулируют изменением подачи газа в коллектор, к которому подключен
данный ряд горелок. Необходимое для горения количество воздуха устанавливают
заслонкой 4 индивидуально для каждой
горелки. Для газа заданного состава такая регулировка необходима лишь при пуске
печи, так как конструкция инжекционного смесителя обеспечивает практически
постоянное соотношение количества газа и воздуха в пределах изменения
теплопроизводительности горелки примерно в 2 раза.
Змеевик
трубчатой печи составляют из прямых бесшовных труб длиной 6-18 м, с наружным
диаметром 60-219 мм. Наиболее часто используют трубы диаметром 102; 127 и 152
мм. Трубы соединяют в непрерывную цепочку специальными печными двойниками с
крышками или без них. Открываемые двойники применяют при температуре до 560 °С,
когда необходима механическая чистка внутреннего пространства труб от отложений
кокса. В печах пиролиза, работающих при более высокой температуре, трубы
соединяют обычно приварными двойниками. Из-за малого расстояния между трубами
((1,8-2,2) d) двойники нельзя изготовлять из трубы
гибкой; их получают протяжкой труб или сваркой штампованных половин. В этом
случае трубы очищают от кокса выжиганием. Для этого в трубы подают смесь,
состоящую из одной части воздуха и десяти частей водяного пара.
Материал
труб змеевика выбирают в зависимости от температурного режима и коррозионных
свойств сырья, причем в различных зонах печи используют трубы, из разных
материалов. Так, в печах пиролиза начальные участки змеевика, расположенные в
конвекционной зоне, работают при температуре 30-400 °С, а конечные, находящиеся
в радиантной камере, - при температуре 500-900 °С. По этой причине
конвекционные трубы первых рядов изготовляют из углеродистых стальных труб
(20Г), последних рядов - из хромомолибденовой стали (15Х5М), а радиантные трубы
- из жаропрочной стали 12Х18Н10Т. 268
Для
крепления труб змеевиков в печах используют подвески кронштейны различных
конструкций. Для той же цели по торцам печи устанавливают две трубные решетки в
виде вертикальных прямоугольных листов с отверстиями для труб. Трубные ре-щетки
теплоизолируют со стороны, обращенной в сторону топочной камеры. Подвески располагают
на расстоянии 0,8-3 м одна от другой, в зависимости от температуры труб.
Подвески, кронштейны и трубные решетки радиантной камеры,
работающие при температуре до 1000 °С, отливают из жаропрочной стали 20Х23Н13.
В конвекционной камере, где температура ниже, используют подвески из чугуна
СЧ21 или из стали 40Х9С2. Подвески крепят к каркасу печи болтами.