Секционированные
массообмечные устройства. Одно из направлений технического прогресса в
химической, нефтехимической и нефтеперерабатывающей промышленности - разработка
и применение аппаратов большой единичной мощности. До не-давнего времени
повышение эффективности и производительности колонн обеспечивали увеличением их
высоты и диаметра.
Однако с
увеличением диаметра колонны возрастает неупорядоченность движения
взаимодействующих фаз: на тарелке появляются <байпасные> потоки, <мертвые>
зоны, возникает поперечная неравномерность скорости газового потока и высоты
жидкости на тарелке. Все это снижает эффективность массообмена в колонне. В
связи с этим производительность аппарата следует повышать не увеличением
размеров аппарата, а созданием контактных устройств, обладающих высокой
производительностью по жидкости и пару, в частности, продольным и поперечным
секционированием этих устройств.
Известно, что
производительность тарелок повышается при контактировании фаз в прямотоке.
Однако при прямоточном взаимодействии и большой скорости пара (газа) жидкость
смещается в направлении к сливному карману, что затрудняет работу сливных
устройств.
Для компенсации
прямоточного движения фаз и исключения его распространения на всю тарелку можно
устанавливать на тарелке продольные и поперечные перегородки, обеспечивающие
зигзагообразное движение жидкости на тарелке от перелива к сливу, а также
создающие условия для движения потоков парожидкостной смеси по тарелке в
противоположных или пересе-кающихся направлениях.
Примером может служить
продольно-секционированная тарелка с просечными элементами (рис. 14.12). На
полотне тарелки 2 выштампованы просечки 1, отогнутые под углом а. Тарелка
секционирована вдоль потока жидкости вертикальными перегородками 3,
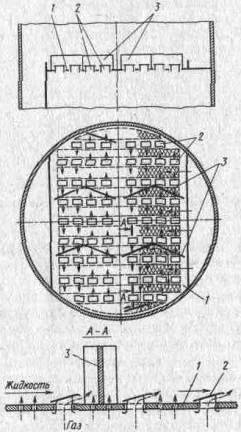
Рис 14.13 Комбинированная
клапанная тарелка
|
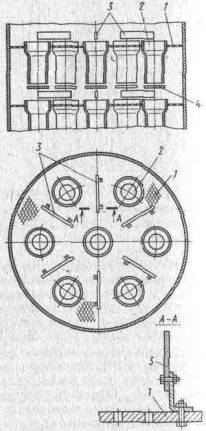
Рис 14.14 Тарелка с двумя
зонами контакта
|
причем для создания постоянного
гидрав-лического сопротивления по всей тарелке перегородки перфори-рованы.
При
скорости газа до 1,5 м/с тарелки работают аналогично ситчатой и колпачковой:
жидкость из переливного кармана а поступает на рабочую часть тарелки, газ
вводится через просечки, барботирует через слой жидкости, аэрирует ее и на
тарелке образуется газожидкостный слой. При скорости газа более 1,5 м/с газовые
струи, выходящие из просечек, и создаваемые ими потоки жидкости движутся к
вертикальным перегородкам или стенкам колонны, Ударяются о них, сепарируются и
газ покидает тарелку. При этом жидкость совершает сложное зигзагообразное
движение от переливного а к сливному 6 карману.
Вариантом
массообменного устройства с продольным секционированием является клапанная
тарелка с продольными перегородками 3 (рис. 14.13), которая отличается от
тарелки с просеч-ными элементами тем, что на полотне 1 тарелки вместо просечек
смонтированы клапаны 2 с боковыми стенками, обеспечивающие направленное
движение жидкостного потока.
По
производительности такие тарелки превосходят обычные клапанные тарелки без
продольного секционирования в 1,4 раза, а по эффективности массообмена в
1,25-1,3 раза;
При высокой
плотности орошения [более 50 м3/(м2ч)], когда работа
тарелок лимитируется производительностью переливных устройств, целесообразно
применение многосливной продольно-секционированной тарелки, или тарелки с двумя
зонами контакта фаз (рис. 14.14). Последняя представляет собой комбинацию
барботажной тарелки (ситчатой, клапанной) с устройством, в котором реализуется
зона контакта фаз, формирующаяся в пространстве между тарелками при перетекании
жидкости. Тарелка состоит из перфорированного основания 1 с установленными на
нем сливными карманами 2 (могут быть одно-, двух- и трехщелевьми), направляющих
планок 3 и отбойных дисков 4.
Однощелевой
сливной карман, установленный на тарелке 1 (рис. 14.15, а), состоит из патрубка
2 и отбойного диска 3, укрепленного так, что между ними образуется кольцевая
щель шириной hщ = 4 ...
12 мм. Через эту щель вытекает кольцевая струя жидкости, образуя дополнительную
зону контакта. При установке двухщелевого сливного кармана (рис. 14.15, б)
жидкость переливается через сливную перегородку, протекает по внутренней стенке
наружного патрубка 2 и конусу 4 во внутренний патрубок 5 и вытекает из нижней
щели кольцевой струей, образуя дополнительную зону контакта.
С
увеличением производительности по жидкости уровень ее в патрубке 5 повышается,
жидкость заполняет пространство в патрубке 2 и начинается истечение из верхней
щели. В пространстве между тарелками образуется вторая кольцевая струя. Таким
образом, многощелевой слив позволяет значительно расширить диапазон нагрузок по
жидкости
Насадочные колонные аппараты
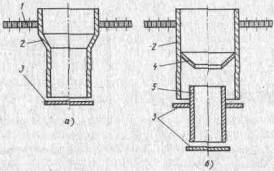
Рис. 14.15. Однощелевые (а) и
двухщелевые (б) карманы
|
Диаметр
насадочных колонн обычно не превышает 4000 мм. Для колонн большого диаметра
трудно достичь высокой эффективности из-за сложности обеспечения равномерного
распределения газовой и жидкой фаз по сечению аппарата. Однако известны
отдельные конструкции насадочных аппаратов диаметром до 12 м.
Корпус 1
абсорбционной насадочной колонны (рис. 14.16) выполняют либо цельносварным,
либо из отдельных царг с приварными или съемными крышками. Насадочные аппараты
весьма чувствительны к неравномерности орошения, поэтому жидкость для орошения
насадки подается через распределительную тарелку 2. Насадку 3 располагают по
высоте аппарата в несколько слоев (секций) и укладывают на опорные решетки 4.
Для загрузки и выгрузки насадки в верхней и нижней частях каждой секции обычно
устанавливают люки б и 8. При больших нагрузках по газу и перепаде давлений
400-700 Па на 1 м высоты насадки сверху на каждый слой насадки укладывают
удерживающую решетку, предотвращающую выброс насадки. В верхней части колонны
размещено отбойное устройство 7. Газ и жидкость движутся в насадочной колонне
противотоком. При этом газ вводится в колонну снизу через штуцер А, а выводится
через штуцер Б, орошающая жидкость вводится сверху через штуцер В, а выводится
через штуцеры Г или Д.
При
стекании жидкости по насадке происходит ее перераспределение и на некотором
расстоянии от распределитель, ной тарелки равномерность орошения может резко
уменьшиться; при этом жидкость течет вдоль стенки аппарата, а центральная часть
насадки остается неорошенной. Для исключения этого явления насадочное
пространство разделяют на слои и устанавливают между слоями
перераспределительные тарелки 5, которые собирают жидкость и распределяют ее
вновь по сечению аппарата.
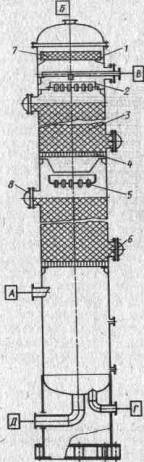
Рис.14.16 Схема
насадочной колонны
|
В настоящее время
используют насадки различных видов. По существующей классификации их можно
отнести либо к регулярной (правильно уложенной), либо к нерегулярной (засыпано:
навалом).
Корпус и
внутренние устройства серийно выпускаемых насадочных аппаратов изготовляют из
тех же материалов, что для тарельчатых массообменных аппарате; Нерегулярную
насадку применяют в процессах массообмена, протекающих под давлением или в
условиях неглубокого вакуума. Эта насадка обладает рядом преимуществ, одно из
которых состоит в практическом отсутствии проблемы выбора материала. Насадку
можно изготовить из металлов, полимеров, керамики. Полимерная и керамическая
насадка наиболее приемлема для обработки агрессивных сред. Нерегулярная насадка
имеет существенные преимущества по сравнению с регулярной по технологии
изготовления, транспортирования и монтажа.
По конструктивным
признакам эту насадку можно разделить на кольца и седла, хотя в
отечественной и зарубежной практике применяют насадочные тела и
другой формы.
В
настоящее время в отечественной химической и нефтехимической промышленности
наиболее распространена нерегулярная насадка в виде колец Рашига и их модификаций.
Насадка Рашига имеет небольшую стоимость, но малоэффективна. Эти кольца из
металла, фарфора, керамики, пластмасс изготовляют самых различных размеров
(диаметр 5-150 мм), хотя в промышленных колоннах чаще используют кольца
диаметром 25 и 50 мм (рис. 2.27, а). Кольца меньшего размера обладают
значительным гидравлическим сопротивлением, большего размера менее эффективны.
Для
повышения эффективности массообмена кольцевую насадку изготовляют перфорированной и с внутренними
перегородками.
В ФРГ предложена кольцевая насадка
размером 50x50 мм коррозионно-стойкой стали - так называемые кольца Палля (рис.
14.17, б). На цилиндрической поверхности насадки выштампованы и отогнуты
вовнутрь лепестки шириной 10 мм. Механическую прочность насадки обеспечивают
кольцевые гофры, служаще также для перераспределения жидкости.
Разновидностью
колец Палля является выпускаемая в США насадка <Хай-пак>, отличающаяся от
рассмотренной числом и расположением лепестков. К кольцевой насадке с
перфорированной цилиндрической частью и внутренними перегородками относится
насадка <Каскад-мини-ринг> (рис.14.17, в).
Отечественная
промышленность изготовляет кольцевую нерегулярную насадку в форме колец Рашига,
а также кольца Палля из пропилена размерами 50x50 мм и из металла размерами
25х25 и 35x35 мм.
Седлообразная
насадка имеет большую удельную поверхность и высокую способность к
перераспределению жидкости по сечению колонны. Такую насадку выпускают главным
образом виде седел <Инталокс> (рис. 14.17, г) и Берля из керамики и пластмассы.
Пластмассовая насадка <Сюпе торус садлес> отличается от седла <Инталокс>
наличием отверстий в центре седла, что повышает ее эффективность, и гофр на
краях, улучшающих перераспределение жидкости.
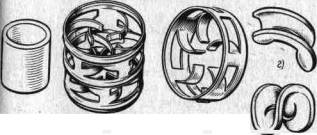
Рис 14.17 Нерегулярные насадки
|
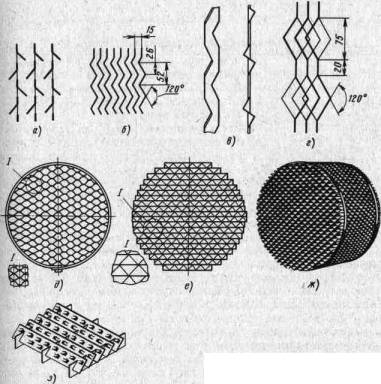
Рис 14.18 Регулярные насадки
|
Регулярная
насадка (правильно уложенная) отличается от нерегулярной меньшим гидравлическим
сопротивлением и поэтому особенно пригодна для процессов вакуумной
ректификации. К недостаткам аппаратов с регулярной насадкой нужно отнести их
высокую чувствительность к равномерности орошения.
Простейшая
регулярная насадка - плоскопараллельная (рис. 14.18) - представляет собой
пакеты, набираемые из плоских вертикальных, обычно металлических пластин
толщиной 0,4-1,2 мм, расположенных параллельно с одинаковым зазором 10- 20 мм.
Высота пакета пластин 400-1000 мм. Наружный диаметр пакета соответствует
внутреннему диаметру колонны Dв.
Для повышения равномерности распределения жидкости в колонне пакеты
устанавливают один над другим взаимно повернутыми на угол 45-90°. Насадка может
устойчиво работать в широком диапазоне производительности по газу [F = 3,5 ... 8 (м/с)/(кг/м3)05]
и по жидкости [L =
0,3 ... 50 м3/(м2-ч)1. В зависимости от
производительности насадка обеспечивает высоту, эквивалентную одной
теоретической ступени, в пределах 0,6-1,5 м при гидравлическом сопротивлении 1
м насадки 70-300 Па. Недостатки этой насадки - высокая металлоемкость, плохое
перераспределение жидкости, сравнительно низкая эффективность. Для устранения
последнего недостатка листы плоскопараллельной насадки выполняют с рифлением
или с различными турбулизирующими элементами. Так, насадка конструкции ЛТИ им.
Ленсовета (рис. 14.19, а) состоит из вертикальных, параллельно расположенных
листов, имеющих поперечные окна с отогнутыми лепестками; соседние по высоте
лепестки отогнуты в противоположные стороны и делят колонну в продольном
направлении на контактные камеры. Газ, поднимаясь по колонне, проходит через
камеры, многократно меняя направление движения при ударе о лепестки. Жидкость,
стекая по насадке с лепестка на ле-песток, распыляется восходящим газовым
потоком.
Основное
преимущество гофрированной насадки (рис. 14.18, б), состоящей из вертикальных
металлических листов с рифлением, по сравнению с плоскопараллельной насадкой -
меньший брызгоунос. Это объясняется тем, что гофрированная насадка
беспровальна. Зазоры между листами иногда обеспечивают дистанциоными планками
(рис. 14.18, б), установленными вертикально на расстоянии 250 мм одна от другой
и приваренными к листам точечной сваркой.
Разновидностью
гофрированной насадки является Z-образная насадка, изготовляемая из перфорированного листа (рис.
14.18, г). По основным технологическим параметрам эта насадка на 15- 20 %
превосходит плоскопараллельную.
Щелевая, или
сотовая насадка (рис. 14.18, д) образована из гофрированных вертикальных
листов, сдвинутых один относительно другого так, что по высоте пакета
образуются изолированные вертикальные каналы. Листы соединены в пакеты высотой
400-1000 мм точечной сваркой. К преимуществам этой насадки относятся значительно
более высокая (в 2-3 раза), чем плоскопараллельной насадки, удельная
поверхность, а также возможность нагревать или охлаждать контактирующие фазы,
поскольку каналы, образованные гофрами, пригодны для подачи в них теплоносителя
или хладагента. К недостаткам насадки следует отнести неравномерность толщины
пленки жидкости в канале. Накопление жидкости в углах канала несколько ухудшает
эксплуатационные качества этой насадки.