|
Лекция 10
Тема: Компелктация и
сборка Механизмов и машин
Комплектация и сборка машин и механизмов.
Сборку начинают со сборки деталей в сборочные единицы, механизмы. На ремонтных заводах сборка осуществляется тупиковым или поточным методом.
При тупиковом методе машина от начала до конца сборки находится на одном месте, как бы в “тупике”, а детали и механизмы подаются к ней на сборку. Этот метод используется при ремонте разнотипных машин при небольшом количестве каждого типа.
При поточном методе основание машины (станина, рама) в процессе сборки перемещается от одного сборочного места к другому. Этот метод применяется при большом количестве однотипных машин и позволяет применять средства автоматизации и механизации ремонтных работ.
Порядок сборки определяется конструкцией машины, ее чертежами и ТУ на ремонт и изготовление. При этом сложность сборки заключается не столько в соблюдении ее последовательности, сколько в контроле взаимного положения деталей. Работоспособность любого узла определяется качеством сборки, т.е. степенью контроля взаимного положения деталей (соблюдение зазоров и посадок, перпендикулярности и параллельности осей). Необходимость выполнения пригоночных и контрольных операций при сборке приводит к тому, что трудозатраты на эту операцию составляют для некоторых машин 50% общих трудозатрат на ремонт.
Во время сборки: проводить регулировку местоположения деталей и узлов.
Сборка резьбовых соединений включает: подачу деталей, наживление (вручную), подвод инструмента, завинчивание, затяжку, отвод инструмента, затяжку, сохранение для предохранения от самоотвинчивания.
При постановке шпильки. Она должна иметь плотную посадку, а ее ось перпендикулярна к поверхности детали в которую она завинчена. Для ее ввертывания служит ручной и механизированный шпильковерт.
Винтовые соединения собираются с предварительной затяжкой. Необходимый момент затяжки резьбового соединения достигается применением динамометрических ключей. Затяжку групповых резьбовых соединений следует выполнять в 2-3 приема в определенном порядке.
Резьбовые соединения, работающие при циклических нагрузках и вибрации стопорят: контрогайками, деформируемыми и пружинными шайбами, разводными шплинтами или проволокой.
Сборку шпоночных и шлицевых соединений выполняют после тщательного осмотра соединительных деталей. На их поверхностях не должно быть заусениц и забоин. Применяют призматические, сегментные и клиновидные шпонки.
Последовательность сборки: сначала шпонку устанавливают легкими ударами медного молотка в паз вала, а затем на вал насаживают схватывающую деталь(шкив, звездочку, шестерню, и т.д.). в паз вала шпонки (призматические, сегментные) должны входить с натягом а в паз схватывающей детали – с некоторым зазором. Клиновидные шпонки-с натягом в паз вала и схватывающей детали. Уклон шпонки и паза в охватывающей детали должен совпадать, т.к. в противном случае возможен перекос.
Разъемные подшипники скольжения (состоящие из двух половинок (вкладышей)), пришабривают к шейкам вала и после сборки проверяют на легкость вращения. При тугом вращении вала ослабляют затяжку болтов и определяют, какой подшипник защепляет вал. Зазор между шейкой вала и вкладышем регулируется установкой прокладок из жести между крышкой и корпусом подшипника. Вкладыши фиксируются штифтами и заплечиками.
При сборке подшипников качения возможны следующие дефекты:
Овальность внутреннего кольца радиального подшипника – как следствие неправильной напрессовки на вал.
Выкрашивание краев колец – из-за их перекоса.
Нагрев подшипника– из-за проворачивания колец на валу или в корпусе.
Появление вибрации – тоже как следствие проварачивание колец.
При сборке необходимо следить, чтобы неподвижное клоьцо имело возможность само устанавливаться для компенсации температурных удлинений.
Подшипники качения сопрягаются с валом и корпусом на подвижных и неподвижных посадках. Если вращается вал, то посадка внутреннего кольца подшипника на вал должна быть неподвижной, а наружного кольца – подвижной (и наоборот при вращающемся корпусе неподвижная посадка применяется для установки наружного кольца, а подвижная наоборот для внутреннего). Подвижность одного из колец позволяет: легко разобрать соединение; устраняет прогиб вала и монтажные ошибки, предупреждает защемление шариков или роликов в подшипнике.
При посадке (или снятии) подшипников на вал или в корпус необходимо соблюдать такие правила: усилие напрессовки (снятия) должно передаваться
через одно из колец, которые туго насаживается, или через оба кольца одновременно без перекоса. Удары непосредственно по кольцам недопустимы. При запрессовке подшипников часто необходим их нагрев в масленой ванне до температуры 80 – 100С.
При сборке валов выполняются следующие операции: валы располагают по установочным размерам и отметкам, затем проверяют горизонтальность и вертикальность положения валов, их параллельность, перпендикулярность или соосность. Биение валов после их центровки не должно превышать для машин среднего класса точности 0.01-0.02 мм.
Сборка зубчатых передач включает следующие операции: проверку взаимного положения валов, насадку и закрепление колес; обеспечение необходимого радиального и бокового зазора; проверку касания рабочих поверхностей зубьев. Величины радиальных и боковых зазоров, а также пятна касания на рабочих поверхностях обязаны соответствовать допускам, установленным техническими условиями.
При сборке червячных передач основное внимание обращается на правильность зацепления червяка с зубьями колеса. При этом средняя плоскость зубчатого колеса должна совпадать с осью червяка, межцентровое расстояние должно точно соответствовать чертежу, а боковой зазор в зацеплении техническим условиям.
Сборка ременных передач сводится к установке, проверке и исправлению взаимного положения подшипников, валов, осей и к навешиванию ремней.
Контроль и испытания при ремонте.
Все ремонтные операции сопровождаются контролем. Например: при межремонтным обслуживании – определяются зазоры в сопряжениях; при дефекации деталей – определяется отклонение деталей от первоначальной формы.
Методы контроля:
- визуально – определяется состояние крепежных деталей, предохранительных механизмов, рабочих поверхностей, наличие трещин, следов коррозии, надломов.
- на слух – шум при работе машины, стуки в сочленениях.
При выполнении сборочных работ используется разнообразный измерительный инструмент и различные методы контроля. Любая операция соединения узлов или деталей должна сопровождаться контролем. Иногда достаточно визуального контроля. В других случаях приходится использовать измерительный инструмент.
Специальные методы контроля, используемые при сборке оборудования в процессе ремонта, охватывают проверку следующих видов геометрического расположения деталей машины:
- прямолинейность плоскостей и горизонтальность различных элементов;
- параллельность осей и плоскостей;
- перпендикулярность осей и плоскостей;
- соосность деталей с осевой симметрией.
Проверка плоскости детали производится с помощью струны, линейки или плиты с выверенной поверхностью.
Для получения осевых линий по которым измеряется взаимное положение узлов и деталей, применяется тонкая ( d = 0.3 до 0.5 мм) натянутая в виде струны стальная проволока. Для натяжки используют груз (10-20 кг). Блок, через который перекинута струна, с помощью суппортов (основная часть металлорежущего стакана – для перемещения режущего инструмента) может перемещаться в горизонтальном и вертикальном направлениях.
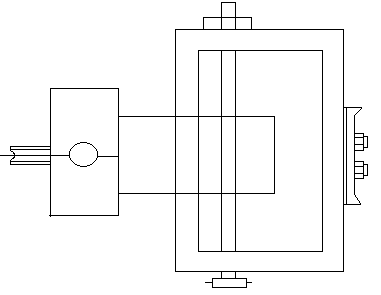
по вертикале (вид сбоку) по горизонтали (вид сверху)
При определении горизонтальности пользуются линейкой и неветиром или гидростатическим уровнем.
Гидростатический уровень позволяет наметить горизонтальную линию, определить различие в высоте двух частей машины или двух половинок фундамента, наметить необходимый уклон и т.д.
Параллельность осей и плоскостей проверяется с помощью натянутых струн, отвесов, штихмассов и других приспособлений.
(штихмасс – измерительный прибор с микрометрической шкалой)
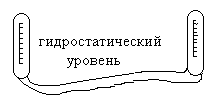 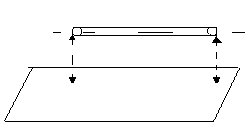
Соосность двух валов измеряется с помощью стрелок. Осевые и радиальные стрелки измеряют с помощью щупа в четырех положениях вала при его повороте на 90гр. При соосности А и В должны быть одинаковы во всех измерениях.
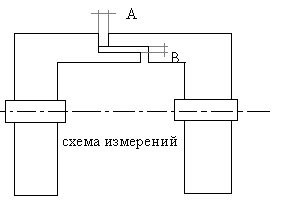
Менее точная проверка ведется по наружной поверхности полумуфт с помощью металлической линейки и щупа. При соосности металлическая линейка должна ложится без зазора на обе полумуфты. Расстояние между торцевыми поверхностями полумуфт в четырех точках, смещенных по окружности на 90гр. должны быть одинаковы.
При проверке параллельности вала на свободных их концах устанавливаются специальные стрелки и перпендикулярно осям валов натягивается струна. Вначале струна должна быть перпендикулярно оси одного вала т.е. А1=А2 (после поворота вала 180гр.) за счет струны. Далее определяются размеры В1 и В2 на втором валу. Если В1=В2-валы параллельны. В противном случае вал сдвигается.
Проверка зазоров в подшипниках качения выполняется индикатором. Для этого внутренне кольцо устанавливают на оправку. К наружному кольцу подводят измерительный штифт индикатора, а с другой стороны прикладывают силу, “выбирающую” полностью люфт. Отклонение стрелки индикатора дает величину радиального зазора.
При проверке осевого зазора измерительный штифт индикатора подводят к торцу наружного кольца. С противоположной стороны легким усилием перемещают кольцо на полную величину люфта.
Равномерность прилегания (разновидность проверки плоскости) наиболее часто контролируется для вала и вкладыша подшипника скольжения, т.е. для деталей цилиндрической формы.
Проверка прилегания производится на краску при повороте вала на 1-1.5 оборота и оценивается количеством пятен на квадрате 25х25 мм. (пятно отпечатка должно занимать не< 80% поверхности постели).
Например, для подшипников компрессоров количество пятен должно быть не менее 20. общая площадь пятен должна превышать 35-40% всей поверхности прилегания.
Другой способ проверки правильности прилегания – с помощью щупа (толщиной 0.05 мм), который не должен проходить в местах соприкосновения вкладыша с постелью.
Правильность прилегания рабочих поверхностей зубьев колес проверяется.
Радиальный и боковой зазоры в передачах с цилиндрическими и коническими зубчатыми колесами проверяются с помощью щупа или свинцовой проволоки, которую прокатывают между колесами. Замерив толщину сплющенных частей проволоки, находят боковой зазор.
Испытание МАХП после ремонта.
Правильность сборки после ремонта проверяется пробным пуском ее вхолостую, вначале медленным проворачиванием в ручную, а затем от электродвигателя. Тяжелые машины прокручивают с помощью троса и лебедки, крана или других приспособлений. Перед пуском должна быть обеспечена полная смазка машины согласно карте смазки, установлены ограждения. Машина должна работать плавно, легко с допустимым шумом, подшипники не должны нагреваться.
Испытание отремонтированной машины проводится в две стадии: холостая обкатка и испытание под нагрузкой. Холостая обкатка проводится для проверки правильности взаимодействия частей и приработке трущихся поверхностей. Длительность холостой обкатки производится инструкцией по испытанию и наладке обор-я.В зависимости от сложности машины длительность обкатки может колебаться от 8 до 72 часов.
Испытание под нагрузкой проводится в соответствии с инструкцией по эксплуатации машины. Нагрузка должна подаваться постепенно в несколько приемов. При каждом увеличении нагрузки испытание проводится в течении 1-3 часов. После достижения номинальной нагрузки проверяются производительность машины, удельные затраты электроэнергии, качество продукции.
Аппараты, работающие под давлением или вакуумом, испытываются на прочность и плотность гидравлически, пневматически или с помощью галоидного течеискателя (для аппаратов глубокого вакуума или работающих с ядовитыми веществами) в соответствии с ведомственными нормалями МН-72-62 и “Правилами устройств и эксплуатации сосудов , работающих под давлением”. После испытания такие аппараты, если это необходимо, должны пройти техосмотр Госгортехнадзора.
Испытания после ремонта (на прочность и плотность).
Для аппаратов, работающих под давлением Р>=0.5 МПа, величина контрольного давления на прочность составляет 1.25*Р.
Испытанию на плотность подвергаются аппараты, предназначенные для работ с горючими, взрывоопасными и токсичными продуктами. Контрольное давление при испытании на плотность должно быть равно рабочему давлению. Испытание на плотность проводят воздухом или инертным газом.
Качество сварных швов в аппаратах, работающих при атмосферном давлении, проверяется смачиванием керосином, а прочность самих аппаратов испытывается водой под наливом. С одной стороны сварной шов покрывают меловой обмазкой, а с другой керосином. Время проведения испытания от 1 до 24 часов. Если в сварке есть дефекты (поры, трещины, шлаковые включения), то на высушенной меловой обмазке появится жирное керосиновое пятно.
Аппараты, работающие под избыточном давлением до 7МПа, испытываются давлением указанным в чертежах.
Аппараты, имеющие рабочую температуру стенки выше 40 С, подвергаются гидравлическому испытанию при давлении, превышающем рабочее не менее, чем в 1.5 раза.
Вакуум-аппараты испытываются гидравлически на прочность избыточным давлением 0.2 МПа и на плотность пневматически избыточным давлением 0.1 МПа.
Контроль утечек при испытании на плотность может быть выполнен промазкой мыльной пеной предполагаемых мест утечки. Фланцевые соединения также промазывают пеной (латексом или специальном составом).
Проверка зазоров в подшипниках качения выполняется индикатором. Для этого внутреннее кольцо устанавливают на оправу. К наружному кольцу подводят измерительный штифт индикатора, а с другой стороны прикладывают силу, “выбирающую” полностью люфт. Отклонение стрелки индикатора дает величину радиального зазора.
При проверке осевого зазора измерительный штифт индикатора подводят к торцу наружного кольца. С противоположной стороны легким усилием перемещают кольцо на полную величину люфта.
Равномерность прилегания (разновидность проверки плоскостей) наиболее часто контролируется для вала и вкладыша подшипника скольжения, т.е. для деталей цилиндрической формы. Проверка прилегания производится на краску при повороте вала на 1-1.5 оборота и оценивается количеством пятен на квадрате 25х25 мм.(пятно должно занимать не <80% поверхности постели).
Например, для подшипников компрессоров количество пятен должно быть не менее 10. общая площадь пятен должна превышать 35-40% всей поверхности прилегания.
Другой способ проверки правильности прилегания – с помощью щупа (толщиной 0.05мм) который не должен проходить в местах соприкосновения вкладыша с постелью.
Правильность прилегания рабочих поверхностей зубьев колес проверяется по краске в местах контакта.
Радиальный и боковой зазоры в передачах с коническими и цилиндрическими зубчатыми колесами проверяются с помощью щупа или свинцовой проволоки, которую прокатывают между колесами. Замерив толщину сплющенных частей проволоки, находят боковой заруб.
Испытание МАХП после ремонта.
Правильность сборки после ремонта проверяется пробным пуском ее в холостую, вначале медленным проворачиванием в ручную, а затем от электродвигателя. Тяжелые машины прокручивают с помощью троса и лебетки, крана ии других приспособлений. Перед пуском должна быть обеспечена полная смазка машины согласно карте смазки, установлены ограждения. Машина должна работать плавно, легко с допустимым шумом, подшипники не должны нагреваться.
Испытание отремонтированной машины проводится в две стадии: холостая обкатка и испытание под нагрузкой. Холостая обкатка проводится для проверки правильности взаимодействия частей и приработке трущихся поверхностей. Длительность холостой обкатки производится инструкцией по испытанию и наладке обор-я. В зависимости от сложности машины длительность обкатки может колебаться от 8 до 72 часов.
Испытание нагрузкой проводится в соответствии с инструкцией по эксплуатации машины. Нагрузка должна подаваться постепенно в несколько приемов. При каждом увеличении нагрузки испытание проводится в течение 1-3 часов. После достижения номинальной нагрузки проверяются производительность машины, удельные затраты электроэнергии, качество продукции.
Аппараты, работающие под давлением или вакуумом, испытываются на прочность и плотность гидравлически, пневматически или с помощью галоидного течеискателя ( для аппаратов глубокого вакуума или работающих с ядовитыми веществами ) в соответствии с ведомственными нормалями МН-72-62 и “Правилами устройств и эксплуатации сосудов, работающих под давлением”. После испытания такие аппараты, если это необходимо, должны пройти техосмотр Госгортехнадзора.
|
|