Предохранительная
и защитная арматура.
Предохранительная
арматура исключает возможность, возникновения недопустимо высокого давления в
трубопроводных системах и на установках. Чаще всего используют
предохранительные клапаны и разрывные мембраны.
Предохранительные клапаны бывают рычажно-грузовыми
(рис. 17.11) и пружинными (рис. 17.12). Нижним штуцером их устанавливают на
трубопроводе или аппарате; через боковой их штуцер отводится избыток среды.
Давление на золотник клапана регулируют изменением числа грузов или силы сжатия
пружины. Грузовые клапаны устанавливают лишь в одном положении, при котором
золотник строго вертикален. Пружинные клапаны монтируют в любом положении.
Грузовой клапан в отличие от пружинного не имеет сальника на штоке, поэтому его
нельзя устанавливать внутри помещений, а также на трубопроводах для
транспортирования огнеопасных сред.
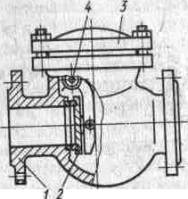
Рис. 17.14. Обратный
поворотный клапан
|
Разрывные
мембраны, устанавливаемые на трубопроводах, срабатывают при повышении рабочего
давления на 20-25 %. Мембраны обеспечивают высокую герметичность, а также
надежность срабатывания; их недостаток - одноразовое использование.
Назначение
защитной (отсечной) арматуры состоит в предотвращении аварийной ситуации в
системах отключением защищаемого участка. К защитной арматуре относятся прежде
всего обратные клапаны (подъемные и поворотные). Назначение обратных клапанов -
защита трубопроводных систем от обратного потока, что может в ряде случаев
создать аварийную ситуацию. В показанном на рис. 17.13 обратном подъемном клапане
для водопроводов золотник 2 находится в положении <открыто>, поскольку сила от
давления поступающей среды преодолевает вес золотника. С прекращением подачи
среды при возникновении обратного потока золотник опускается на седло и клапан
закрывается.
В обратных
поворотных клапанах (рис. 17.14) проходное сечение закрывается диском 2,
поворачивающимся вокруг горизонтальной оси 4.
Такие клапаны менее чувствительны к загрязненности среды, но по
герметичности уступают подъемным клапанам. Для уменьшения скорости закрывания и
исключения возможности гидравлического удара поворотные клапаны большого
диаметра снабжают демпферами, противовесами и др.
Выбор трубопроводной арматуры
Основной тип
запорной арматуры, рекомендуемой для трубопроводов диаметром от 50 мм и более,
- задвижка; она имеет минимальное гидравлическое сопротивление, надежное
уплотнение затвора и допускает изменение направления движения среды. Вентили
рекомендуется устанавливать на трубопроводах диаметром до 50 мм; при диаметре
трубопровода более 50 мм вентили используют главным образом в случаях, когда по
условиям тех-нологического процесса требуется ручное дросселирование. Основное
преимущество вентилей - отсутствие трения уплотнительных поверхностей, что
значительно уменьшает опасность их I повреждения посторонними частицами и позволяет использовать
при более высоких давлениях. В связи с этим вентили устанавливают на
трубопроводах высокого давления.
Краны
используют, когда требуются запорные устройства, обладающие незначительным
гидравлическим сопротивлением или способные управлять несколькими расходящимися
потоками, в последнем случае используют трех-четырехходовые краны.
Дисковые заслонки устанавливают на
трубопроводах для жидких газообразных неагрессивных сред с температурой до 80
°С, при условном проходе до 2000 мм и давлении до 1,6 МПа.; Использование
регулирующей аппаратуры регламентируется требованиями нормативных
документов, а область применения
обратных и предохранительных клапанов - правилами Госгортехнадзора.
При выборе материала для трубопроводной
арматуры прежде всего следует учитывать свойства транспортируемой среды, ее;
коррозионную активность, воспламеняемость, токсичность.
В трубопроводах для горючих, токсичных,
пожаро- и взрывоопасных сред, сжиженных газов применяют только стальную
арматуру.
Арматуру из ковкого чугуна допускается
использовать на газопроводах для горючих газов в диапазоне рабочих температур
от -30 до +150 °С, при давлении до 1,6 МПа, а арматуру из серого чугуна - в
диапазоне рабочих температур от -10 до +100 °С при давлении до 0,6 МПа.
В соответствии с нормативными требованиями,
независимо от среды рабочего давления и
температуры, не рекомендуется
устанавливать чугунную арматуру на трубопроводах: для токсичных веществ группы
А, а также для сжиженных углеводородных газов и легковоспламеняющихся жидкостей
с температурой кипения ниже 45 °С; для газов при возможности вибрации
трубопровода; для газов, содержащих пары воды, и других замерзающих жидкостей
при температуре стенки трубы ниже О °С; для газов; при возможности растяжения
трубопровода; при их размещении на открытом воздухе при температуре воздуха
ниже -30 °С. На трубопроводах, работающих при температуре ниже-40 °С, следует
устанавливать арматуру из легированных сталей и специальных сплавов.
На трубопроводах, предназначенных для
транспортирования высокоагрессивных сред, используют арматуру в
коррозионностойком исполнении.
На трубопроводах для сред с токсичными
свойствами, горючих и активных газов, легковоспламеняющихся жидкостей следует
устанавливать арматуру, удовлетворяющую требованиям повышенной герметичности к
запорным и сальниковым устройствам. В случаях, когда это допустимо, арматуре с
сальниковым уплотнением штока в корпусе, как наиболее дешевой, отдают
предпочтение перед арматурой с сильфонным уплотнением. Для трубопроводов с
токсичной, огне- и взрывоопасной средой выбирают сильфонную арматуру.
Ручное управление арматурой используют
лишь при ее редком срабатывании. При частом использовании арматуры, а также в
условиях автоматизированного управления производственным процессом применяют
арматуру с электро-, пневмо- и гидроприводами. Арматуру с электроприводом не
используют при температуре окружающего воздуха ниже -40 °С, на открытых
площадках и в колодцах с повышенной влажностью.
На
трубопроводах малого (до 80 мм) диаметра арматуру крепят на резьбе, так как
резьбовые соединения требуют минимального числа присоединительных элементов,
просты по конструкции и исполнению. Для ответственных случаев, когда требуется
частый демонтаж системы, например с целью очистки, на трубопроводах малого
диаметра используют фланцевые соединения. Наиболее надежный способ
присоединения арматуры - сварка, поэтому в трубопроводах для горючих,
токсичных, пожаро- и взрывоопасных сред сварку используют везде, где это допустимо.
Во фланцевых
соединениях трубопроводов для сильно действующих ядовитых веществ и дымящих
кислот независимо от давления и температуры конструкцию уплотнительных
устройств выполняют по типу <шип - паз>.
Особенности монтажа и эксплуатации
трубопроводов
Объем
работ по монтажу технологических трубопроводов в общем объеме монтажных работ
при сооружении промышленных объектов весьма значителен и достигает в химической
промышленности 35-40 %, в нефтеперерабатывающей 55-60 % .
Монтажным
работам на месте прокладки трубопроводов предшествуют подготовительные работы в
цехах трубных заготовок, где выполняют разметку, резку и гибку труб,
механическую обработку их торцов и вырезание в трубах отверстий, сборку и
сварку элементов трубопроводов в сборочные единицы, испыта-ния сборочных единиц
трубопроводов, их маркировку и др.
Сваривают трубы
на специальных сборочных стендах с использованием приспособлений (кондукторов и
центраторов), обеспечивающих правильное сопряжение деталей и узлов
трубопроводов.
Режут трубы на
дисковых, ножовочных или токарных станках. Применяют также установку для
газопламенной резки и маятниковую пилу с абразивными армированными кругами.
После выполнения
резки концы труб и края отверстий обрабатывают на специальных станках или
переносными пневмо- и электрошлифовальными машинами. Трубы диаметром до 200 мм
гнут на трубогибочных станках в холодном состоянии, а трубы диаметром более 200
мм - в горячем состоянии. Для уменьшения деформации стенок в процессе гибки
трубы заполняют сухим песком.
Перед
сборкой трубы и детали трубопроводов очищают от загрязнений и обдувают сжатым
воздухом. Детали, покрытые смазочными маслами, расконсервируют одним из
способов: нагревают в камерах или в ваннах с минеральным маслом при тем-пературе
100-120°С, а затем протирают уайт-спиритом или бензином; промывают горячей
водой или моющими растворами.
Прокладке
трубопроводов предшествует разбивка их трасс; при этом с помощью стальной или
капроновой струны и нивелира через каждые 50-200 м размечают прямолинейные
горизонтальные участки с указанием вертикальных отметок оси трубопровода. Затем
отмечают места расположения подвижных и неподвижных опор, подвесок, арматуры,
ответвлений к аппаратам, температурных компенсаторов. После этого приступают к
установке опорных конструкций, которые выверяют по уровню и отвесу.
При монтаже
трубопроводов применяют трубоукладчики, краны, тали и другие грузоподъемные
механизмы. При монтаже внутрицеховых трубопроводов сварные стыки, которые
должны быть доступны для осмотра, удаляют не менее чем на 50 мм от опор или
подвесок; продольный шов сварных труб располагают так, чтобы его было удобно
осматривать; фланцевые соединения располагают непосредственно у опор.
Трубопроводы не должны пересекать оконные и дверные проемы. Над этими проемами
нельзя устанавливать арматуру, фланцевые и резьбовые соединения. Трубы,
проходящие через стены, необходимо устанавливать в патроны, выступающие за
пределы стены на 50-100 мм в каждую сторону. Патроны надевают на трубу до
начала монтажа и заделывают в стены.
Трубопроводы монтируют
обычно сборочными единицами, представляющими собой участок трубопровода с
арматурой, компенса-торами, теплоизоляцией.
В последние годы все шире применяют метод монтажа
оборудования блоками (крупноблочная
технология монтажа), когда несколько единиц оборудования вместе с обвязочными
трубопроводами, арматурой, приборами контроля и управления поступают на
монтажную площадку в готовом виде с заводов-изготовителей. После окончания
монтажных работ проводят гидравлические или пневматические испытания трубопроводов
на плотность и прочность. Пневматические испытания проводят, если невозможно
провести гидравлическое испытание, например, при температуре окружающего
воздуха ниже 0°С или при отсутствии воды на площадке. При испытательном
давлении трубопровод выдерживают в течение 5 мин, затем давление снижают до
рабочего и осматривают трубопровод, обстукивают сварные швы молотком.
Обнаруженные дефекты отмечают на трубопроводе мелом или краской и устраняют
после снижения давления до атмосферного. Результаты испытания на прочность и
плотность считают удовлетворительными, если во время испытаний давление не
уменьшается, а в сварных швах, фланцевых и прочих соединениях не обнаружены
течи.