|
1.
ОСНОВНЫЕ ПРОЦЕССЫ И
ОБОРУДОВАНИЕ
МНОГОАССОРТИМЕНТНЫХ
ХИМИЧЕСКИХ ПРОИЗВОДСТВ
Типовая технологическая
схема производства химических
продуктов состоит из стадий
подготовки сырья, химического
синтеза, выделения и очистки
продуктов.
Примерами стадий
подготовки сырья
производств химических
красителей могут служить
растворение, очистное
фильтрование; химического
синтеза - сульфирование,
нитрование, диазотирование,
азосочетание; выделения и очистки
продуктов - кристаллизация,
суспензирование, фильтрование,
сушка. Практически все стадии
представляют собой
совокупность разнообразных
технологических процессов:
механических,
гидромеханических, тепловых,
диффузионных, химических,
микробиологических.
Совокупность аппаратов, в
которых реализуются
технологические стадии
процессов получения продукции,
называются аппаратурными
стадиями технологических систем.
В многоассортиментных
химических производствах
очень редко используются
специализированные аппараты,
сконструированные для
реализации конкретных
технологических процессов.
Большинство технологических
стадий реализуется в
стандартных аппаратах,
выпускаемых предприятиями
химического машиностроения,
ряды типоразмеров и параметры
стандартных аппаратов
определяются ГОСТами и
содержатся в каталогах.
Оборудование
аппаратурных стадий
подразделяется на основное,
в котором осуществляются
химико-технологические
процессы, сочетающие
химические реакции с
массопереносом (диффузией), и вспомогательное.
Вспомогательные аппараты, в
которых осуществляются
подготовительные операции –
измельчение, растворение,
осушка или увлажнение, нагрев
или охлаждение, промывка и т.п.,
обычно расположены в
технологической схеме как до
реактора, так и после него.
Основное назначение аппаратов,
предшествующих реактору,
заключается в подготовке сырья
к реакции, а аппаратов,
расположенных за реактором, -
разделении продуктов реакции,
концентрировании их или
очистки от вредных примесей.
Иногда вспомогательные
операции (подогрев,
измельчение, растворение,
испарение, конденсация и т.п.), и
собственно химическое
превращение могут происходить
в одном и том же аппарате.
Основное оборудование - это
емкостные аппараты с
перемешивающими и
теплообменными устройствами,
колонны, фильтры и центрифуги,
сушилки; вспомогательное -
мерники, сборники,
теплообменники, насосы,
компрессоры.
Наиболее
распространенный основной
аппарат многоассортиментных
производств - емкостный
аппарат с перемешивающим
устройством и системой
теплообмена (рис. 1). В аппаратах
такого типа осуществляется 90%
химических процессов,
значительная доля процессов
подготовки сырья и выделения
продуктов [2]. Многообразие
химических и физических
явлений, лежащих в основе
разнохарактерных
технологических процессов,
выдвигает самые различные
требования к химическим
ректорам. Однако все без
исключения реакторы должны
удовлетворять следующим
основным требованиям: 1)
обеспечивать наибольшую
производительность и
интенсивность; 2) давать
возможно более высокую степень
превращения при максимальной
селективности процесса; 3)
иметь малые энергетические
затраты не траспортировку и
перемешивание реагентов; 4)
быть достаточно простыми в
устройстве и дешевыми; 5)
наиболее полно использовать
теплоту экзотермических
реакций и теплоту, подводимую
извне, для осуществления
эндотермических процессов; 6)
быть надежными в работе, по
возможности наиболее полно
механизированными и
обеспечивать автоматическое
регулирование процесса.
Химические реакторы
различаются по рабочему
объему, конструкционному
материалу, способам
перемешивания и теплообмена,
наличию или отсутствию
внутренних устройств.
Конструкционный материал
химического реактора в
многопродуктовых системах
выбирают в соответствии со
спецификой его эксплуатации на
основе коррозионных свойств
реакционных сред всех
процессов, которые
предполагается осуществлять в
реакторе, учитывая при этом
возможное изменение исходных
физико – химических свойств
материалов под воздействием
среды, температуры и
протекающих
химико-технологических
процессов. При выборе
материалов для аппаратуры
необходимо руководствоваться
отраслевым стандартом ОСТ
26.291-79. В качестве
конструкционных материалов
наиболее часто применяют:
углеродистую сталь;
нержавеющую сталь Х18Н10Т; сталь
с эмалевым покрытием; сталь,
футерованную керамической
плиткой; титан; иногда
пластические массы, кислото- и
щелочестойкую керамику..
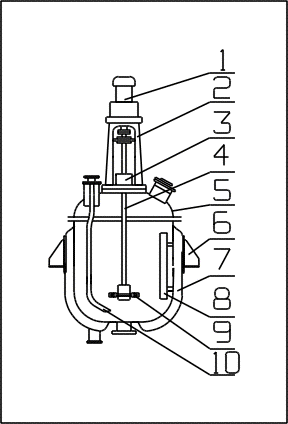 |
В реакторах,
функционирующих в составе
многоассортиментных и
гибких систем, следует
предусмотреть возможность
установки механических
мешалок любого типа из
имеющегося стандартного
набора: лопастные, якорные,
рамные, пропеллерные,
турбинные, - подачу сырья
нескольких видов в
различных агрегатных
состояниях и выгрузку
реакционной массы,
обусловленную перепадом
давлений в аппаратах
(самотеком), насосом или
выдавливанием ее сжатым
воздухом, паром, инертным
газом.
Рис.1.
Емкостный аппарат
1- привод, 2 - стойка
привода,
3 -уплотнение вала,
4 - вал мешалки,5 -
корпус,
6-опора(лапа),7-гладкаярубашка,
8-отражательная
перегородка,
9-мешалка,10-руба ередавливания.
|
|
Для нагревания
реакционной массы реакторы
снабжают греющей рубашкой или
(и) встроенным змеевиком, в
которые подают горячую воду,
насыщенный пар давлением до 0.6
МПа или высокотемпературный
органический теплоноситель.
Охлаждение
реакционной массы и
отвод тепла экзотермических
реакций
осуществляется
хладоагентами, подаваемыми в
рубашку и змеевик. Наиболее
известными хладоагентами
являются артезианская или
оборотная вода, охлаждающие
рассолы.
Определяющий размер
(объем) реактора устанавливают
на основании материального
баланса реактора, а
необходимую поверхность
теплообмена - по уравнениям
теплового баланса. Выполнив
расчет, выбирают реактор из
каталога стандартного
оборудования. 
Вертикальные
цилиндрические стальные
аппараты без покрытий, с
полимерными и другими
покрытиями, футерованные, а
также аппараты из цветных
металлов и сплавов объемом
0.01-100 и
внутренним диаметром 250 – 5000 мм
с механическими
перемешивающими устройствами
регламентированы ГОСТ 20680-75.
ГОСТ распространяется на
аппараты для проведения
различных физико –химических
процессов в жидких средах с
динамической вязкостью не
более 500 Па с и плотностью до
2000 кг/ при температуре от –40 до + С
при условном давлении:
остаточном - не ниже 0.67 Па и
избыточном – не выше 6.4 МПа.
Механические перемешивающие
устройства для вертикальных
аппаратов емкостью 0.01-100 стандартизированы
ГОСТ 20680-75. Согласно ГОСТу,
мешалки должны располагаться
вертикально по оси аппарата, на
одном валу могут быть
установлены две мешалки и
более.
В настоящее время большое
внимание уделяется разработке
конструкций комбинированных
аппаратов
многофункционального
назначения, в которых можно
одновременно или
последовательно проводить
различные процессы (химический
синтез и выделение продукта,
фильтрование и сушку).
Совмещение технологических
процессов в одном аппарате
позволяет сократить число
аппаратурных стадий получения
продукта и, следовательно,
снизить материалоемкость
конструкции, энергетические
затраты, число транспортных
операций и потери
промежуточных продуктов,
упростить обслуживание
оборудования.
По режиму
функционирования различают
аппараты периодического,
непрерывного и
полунепрерывного действия. Функционирование
аппарата периодического действия
представляет собой
циклический процесс:
заполнение, обработка массы,
опорожнение, простой в
ожидании заполнения и т.д.
Упорядоченная
последовательность
технологических и
организационных мероприятий,
имеющих конечную
продолжительность, образует
технологический цикл аппарата,
продолжительность которого
равна сумме длительностей
операций:
(1)
Процесс функционирования
аппаратов периодического
действия изображают в виде
графиков, называемых графиками
Гантта (рис. 2).
Технологические операции
в аппарате периодического
действия подразделяются на
основные, в результате которых
образуется новое вещество или
изменяется состав и агрегатное
состояние системы, и
вспомогательные (загрузка,
выгрузка, простой). Основные и
вспомогательные операции
разделены во времени, т.е.
основной технологический
процесс в аппарате
периодического действия
прерывается вспомогательными
операциями. Основные параметры
процесса в реакторе
периодического действия
(концентрация реагентов и
продуктов реакции,
температура, давление и т.п.)
изменяются во времени. Среднюю
скорость процесса можно
измерить производительностью
реактора. Истинная же скорость
сильно и нелинейно меняется в
течение периода работы
ректора, во-первых, вследствие
понижения концентрации
исходных реагентов (по
логарифмическому закону);
во-вторых, вследствие
неизотермичности процесса
(обычно повышение температуры
в начале периода и понижение в
конце его). На скорость
превращения часто сказывается
также появление новых фаз в
процессе работы такого
реактора. Реакторы
периодического действия
работают, как правило, при
сильном перемешивании
реагентов, близком к полному
смешению, и соответственно при
одинаковой температуре во всем
реакционном объеме в любой
момент времени.
Аппараты непрерывного
действия от пуска до
остановки непрерывно (или
систематическими порциями)
питают исходными веществами и
выводят из них продукты
реакции. Величина, обратная
времени пребывания (времени
контакта), называется объемной
скоростью, которую можно
определить как отношение
расхода материала к полезному
реакционному объему. Таким
образом, объемная скорость
может характеризовать
производительность непрерывно
действующего аппарата.
Аппараты
полунепрерывного действия характеризуются
тем, что сырье поступает в
аппарат непрерывно или
определенными порциями через
равные промежутки времени. А
продукты реакции выгружаются
периодически. Возможна и
непрерывная выгрузка продукта
при периодической подаче
сырья. Такие реакторы работают
в переходном режиме. Основные
параметры процесса изменяются
во времени.
В многоассортиментных
производствах преобладают
технологические аппараты
периодического действия; в
некоторых малотоннажных
производствах в периодических
режимах работает до 90-95%
оборудования
|
|